Capolavori hi-tech
La performance attraverso la leggerezza
- Autore: Claudio Primavesi
- Fotografo: Giovanni Danieli
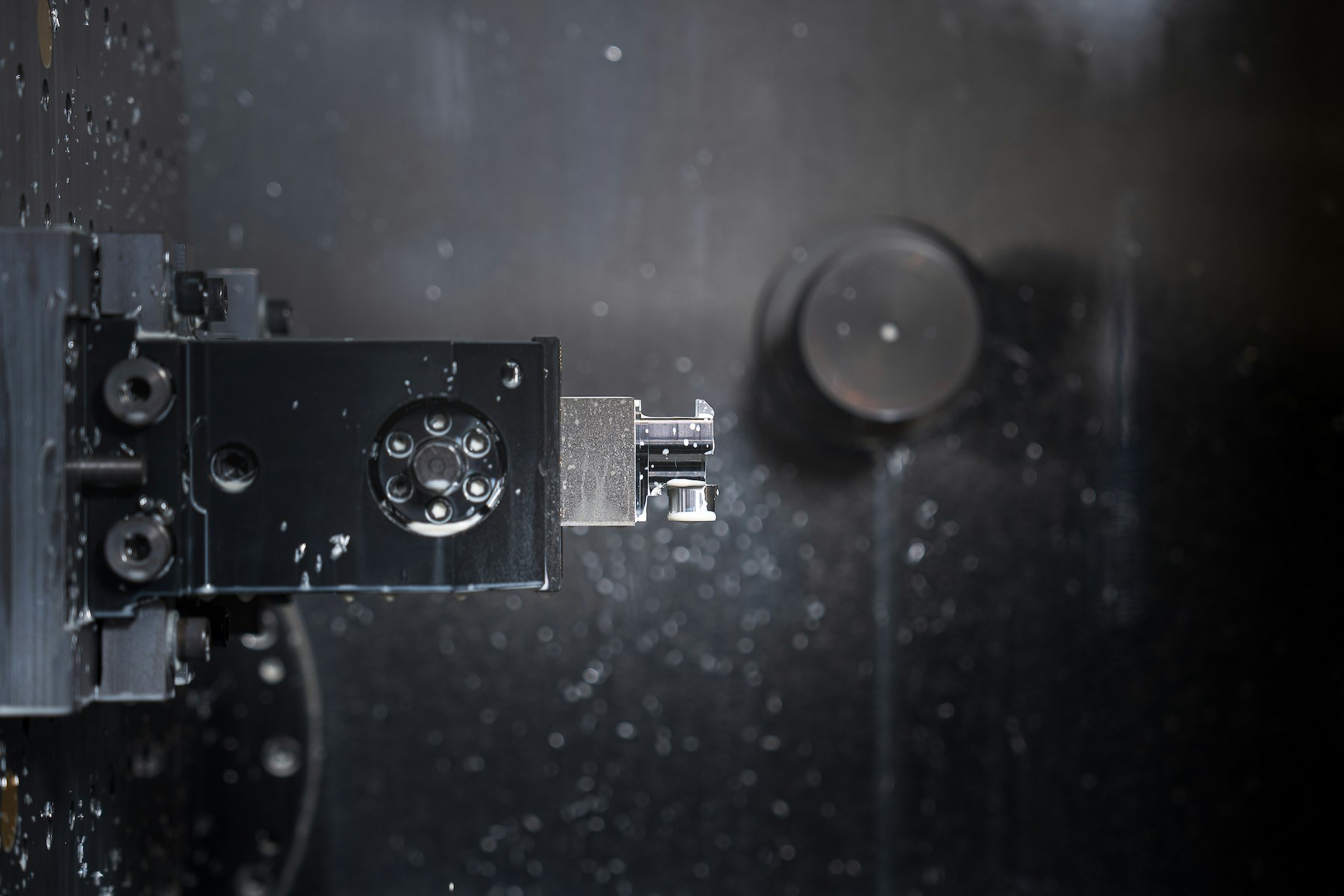
Dopo aver assistito alla produzione da un blocco di alluminio della talloniera di uno dei modelli di punta dell’azienda di Spezzano di Fiorano Modenese, nel cuore della ‘motor valley’ dove ha sede anche la Ferrari, ci si rende conto che il messaggio lanciato nella pubblicità di ATK è vero. Un attacco realizzato con la lavorazione dal pieno è come una scultura. La differenza è che al posto della mano e dello scalpello c’è una fresa hi-tech a cinque assi. Ma, in fin dei conti, rimangono tante affinità. Perché la macchina esegue quello che l’operatore, l’artista della situazione, ha minuziosamente definito. Ce ne siamo accorti quando, sotto i nostri sguardi esterrefatti, nella fresa ha iniziato a prendere forma il logo di Skialper. È stato necessario che quell’idea prendesse forma nella mente di qualcuno e che quella forma assumesse le fattezze di uno schizzo e poi di un disegno al computer.
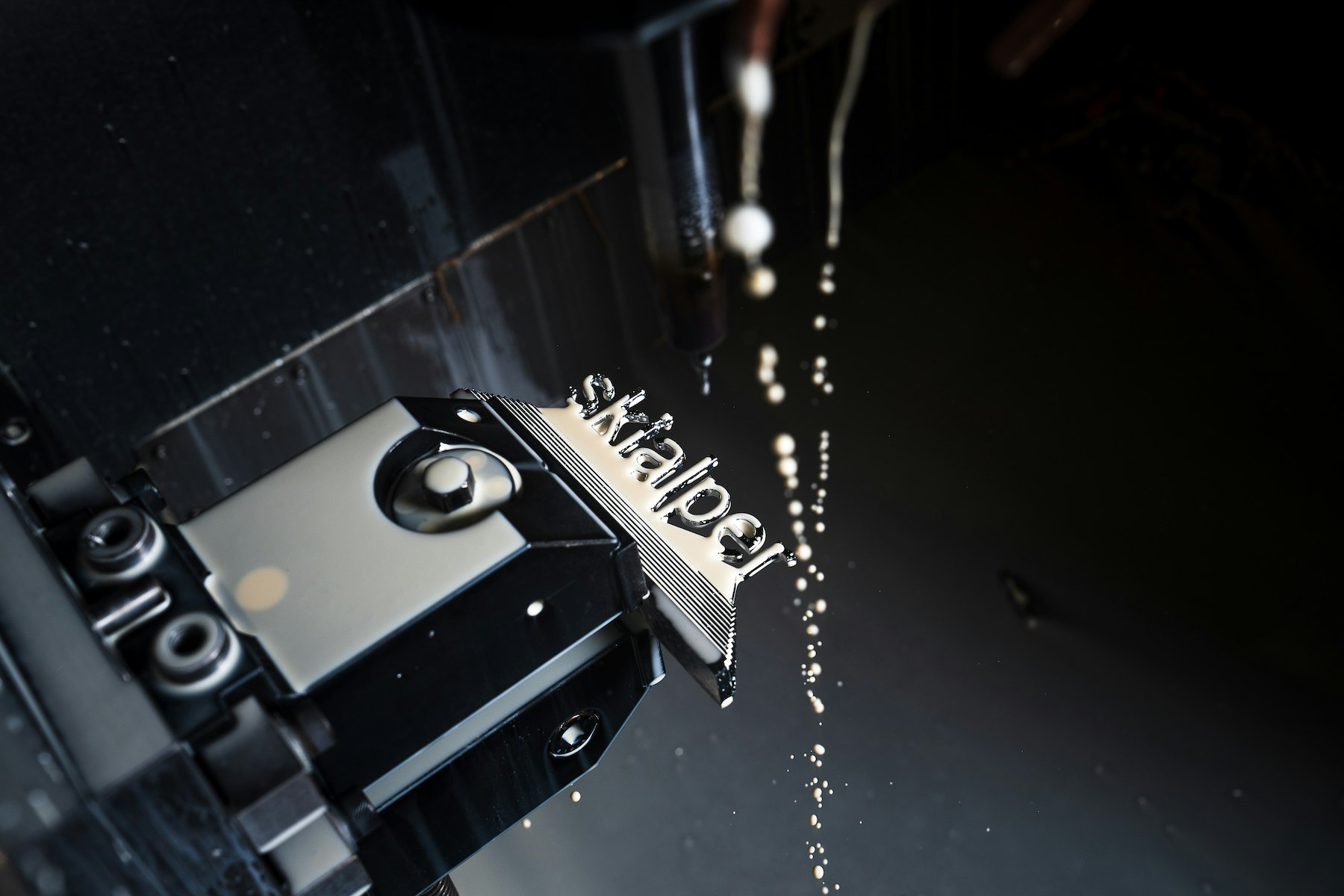
In fin dei conti il segreto di questo miracolo dell’imprenditorialità italiana è tutto qui: aver esportato nel mondo dello scialpinismo e del freeride tecnologie e competenze impiegate in settori di eccellenza come l’industria aerospaziale e l’automotive. Lo dice, senza troppi giri di parole, Davide Indulti, CEO del marchio: «Alla radice della missione di ATK c’è la ricerca dell’estrema precisione unita alla leggerezza, per ottenere un risultato che solo con la lavorazione dal pieno con macchinari a controllo numerico è possibile». Una lavorazione che permette la realizzazione di prodotti di altissima qualità percepita ed effettiva a un costo accettabile grazie all’ottimizzazione del processo produttivo e al riutilizzo massimo degli scarti di produzione e dei componenti necessari, come i lubrificanti. Un plus che, nella visione del futuro che qui hanno sempre avuto, fin dalla produzione del primo pezzo, potrebbe paradossalmente rivelarsi un piccolo problema. È sempre Davide Indulti a sussurrarlo, con una smorfia che disegna un leggero sorriso sulle sue labbra: «Il sogno è di arrivare a riutilizzare gli attacchi per riciclare l’alluminio e dare vita a nuovi attacchi, ma ci rendiamo conto che il valore mantenuto nel tempo dai nostri attacchini e il fatto che, se correttamente mantenuti, funzionino a lungo, è un ostacolo».
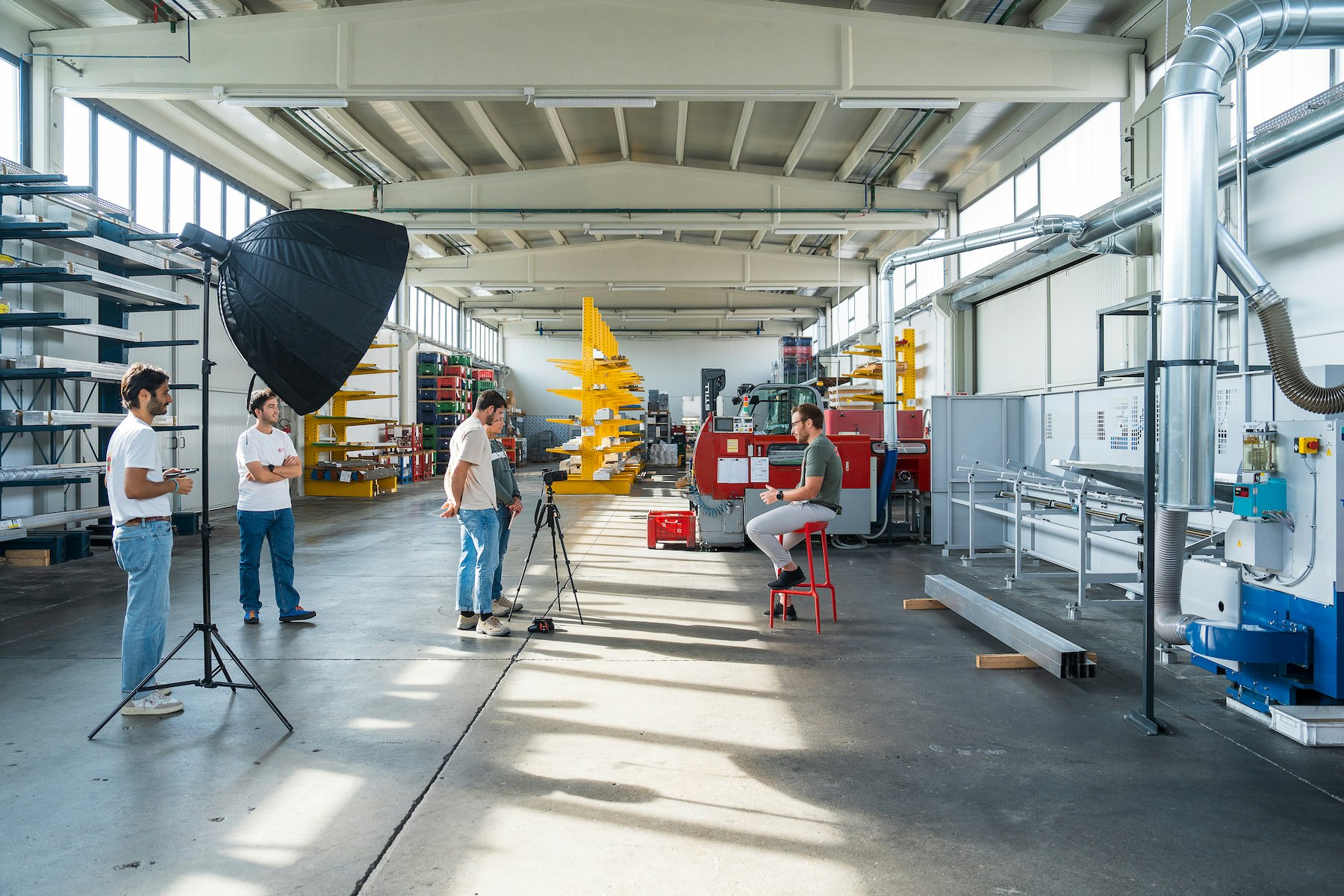
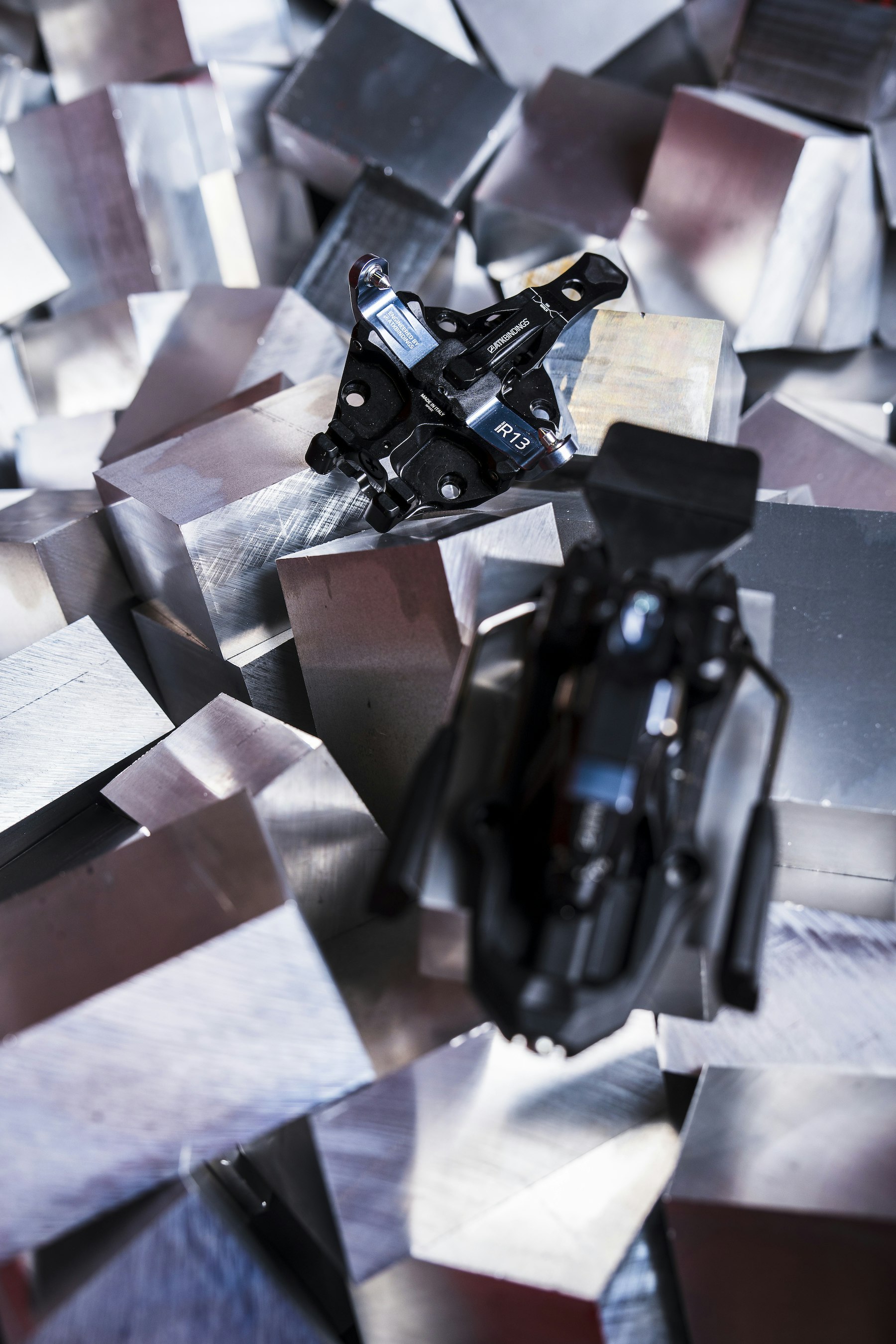
Che poi tanto un ostacolo non è se si pensa che la regola base della sostenibilità è che il prodotto che inquina di meno è quello che dura di più. Paradossi di una visione moderna, oltre gli schemi, che ha permesso a questo marchio della profonda pianura modenese, dove si respira cultura hi-tech o, a pochi chilometri di distanza, agricola e alimentare, di diventare il riferimento mondiale per gli attacchi a pin, portando lo spirito della montagna a fondersi con quello di uno dei distretti industriali più importanti del mondo.
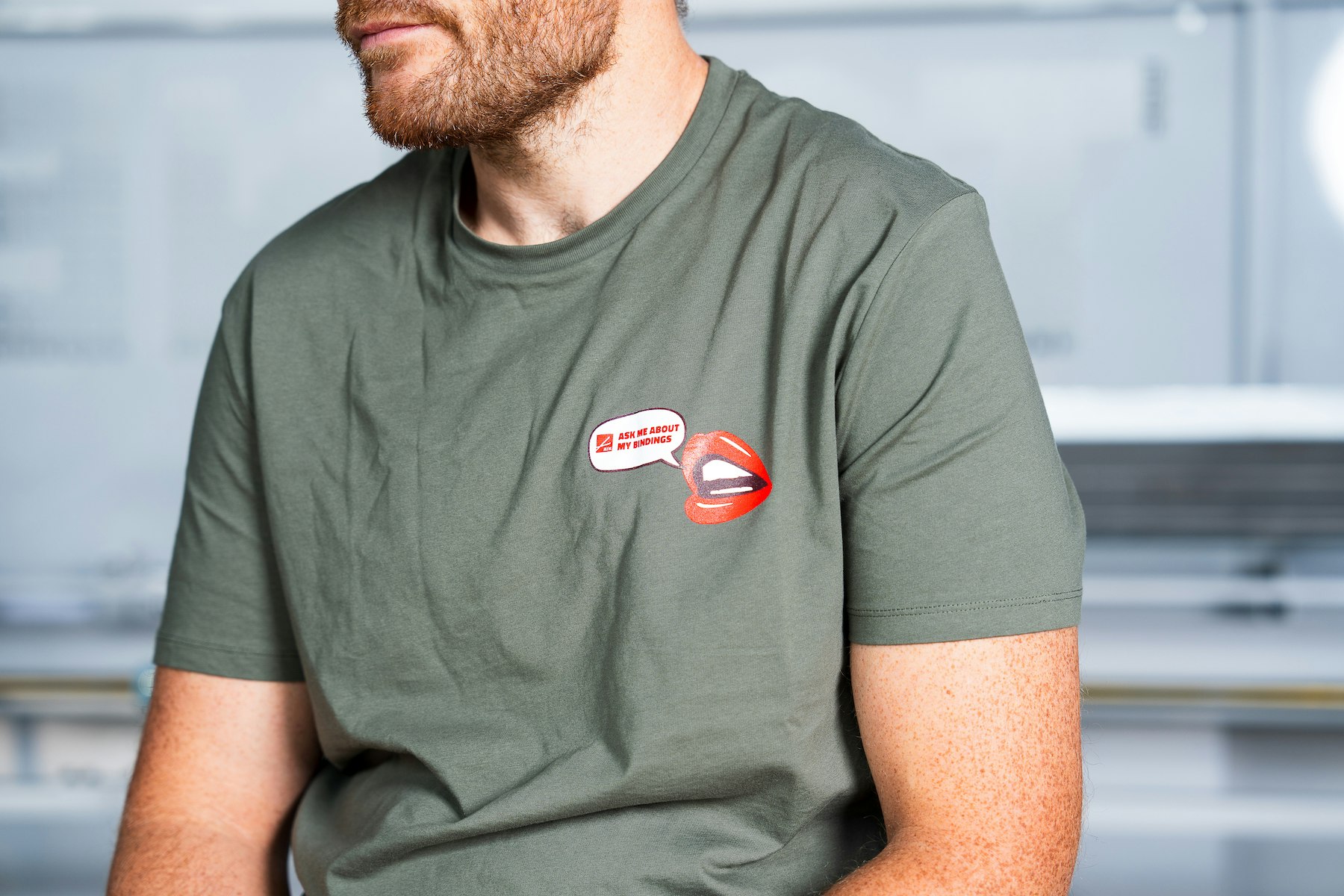
Si può capire molto della filosofia ATK solo leggendo il claim aziendale: Performing through lightness. La performance attraverso la leggerezza. Quella parola magica, leggerezza, che agli inizi della storia di ATK, quando togliere 10 grammi di peso a un modello da gara, con una tecnologia sconosciuta nel settore, era una vera e propria rivoluzione, è rimasta inscindibilmente legata alla missione del marchio, anche in anni in cui la leggerezza non è più un valore fine a se stesso, ma solo se legata alla sciabilità. Appunto, la performance attraverso la leggerezza.
Davide Indulti
Un concetto semplice da esprime, quanto difficile da realizzare. Perché in mezzo c’è un percorso di 15 anni di continuo sviluppo, rimanendo fedeli all’idea originaria: l’attacco a pin. Ci sono brevetti come il CAM Release System che rende una talloniera a spine stabile alla torsione quasi quanto una step-in. Ci sono magazzini pieni di barre di alluminio dei migliori fornitori che diventano da 20 a 45 pezzi che andranno a comporre gli attacchi. Ci sono decine di milioni di euro investiti ogni anno in nuovi macchinari, con 15 frese per la lavorazione dal pieno. Ma ci sono anche tante professionalità e un’età media di 30 anni, il know-how per controllare tutto il processo e occhi che hanno sempre guardato al futuro.
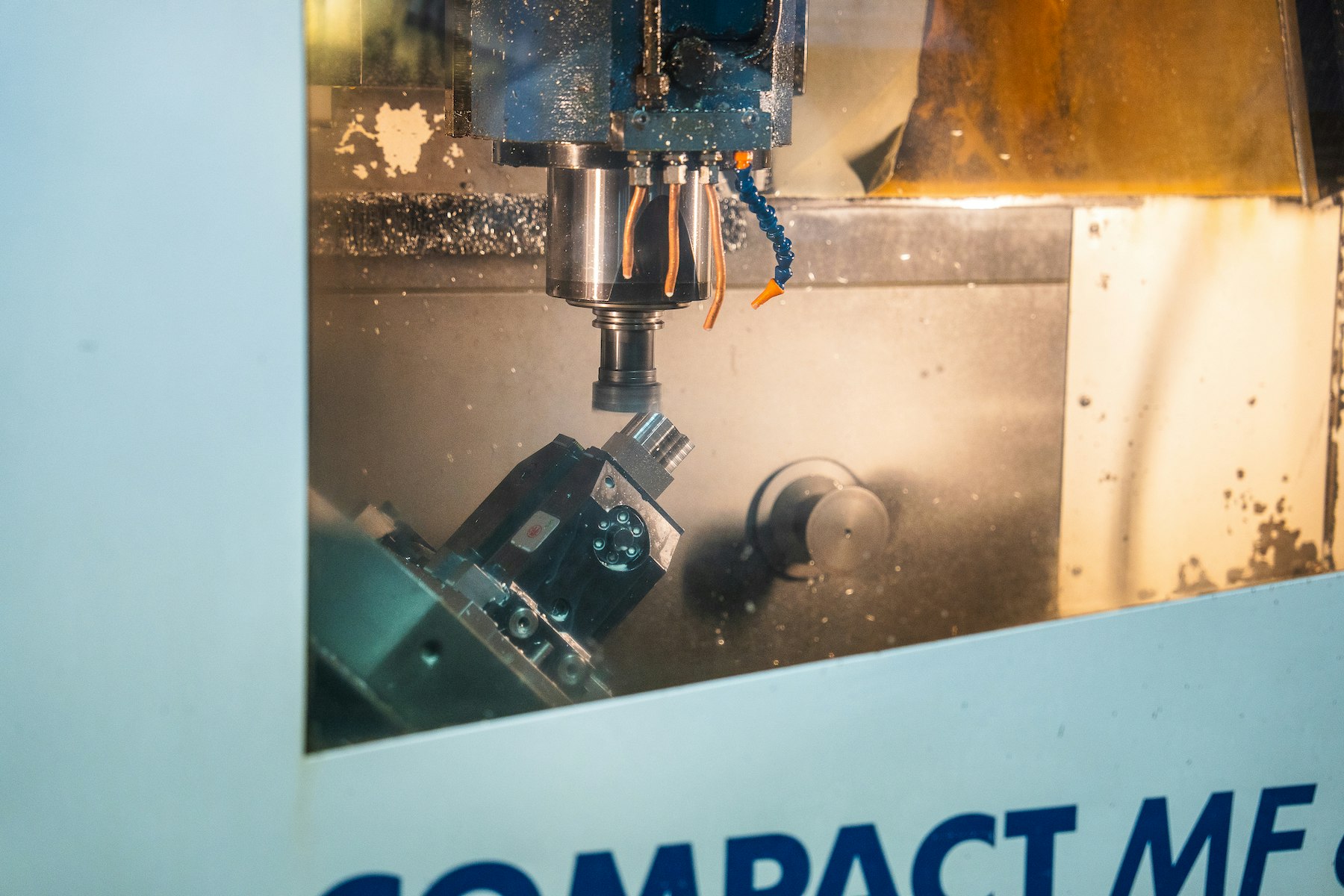
Eravamo già stati in ATK un anno fa. In 12 mesi abbiamo visto due nuove stampanti 3D in grado di produrre il prototipo di un attacco in alluminio e acciaio inossidabile in una notte. Un attacco già sciabile, al netto delle differenze di peso. E poi un macchinario che stampa direttamente il numero di scatole necessarie per il lotto di produzione di uno specifico modello di attacco, evitando sprechi ed errori. Sprechi che sono garantiti anche dall’utilizzo dell’86% di cartone riciclato, riciclabile al 100%, e dalla riduzione al minimo delle etichette. Perfino le istruzioni di montaggio vengono stampate sulla scatola. Sembra non esserci più nulla da inventare. Sembra… A confermarcelo è Davide Indulti mentre ci saluta sull’uscio del capannone dedicato al montaggio degli attacchi.
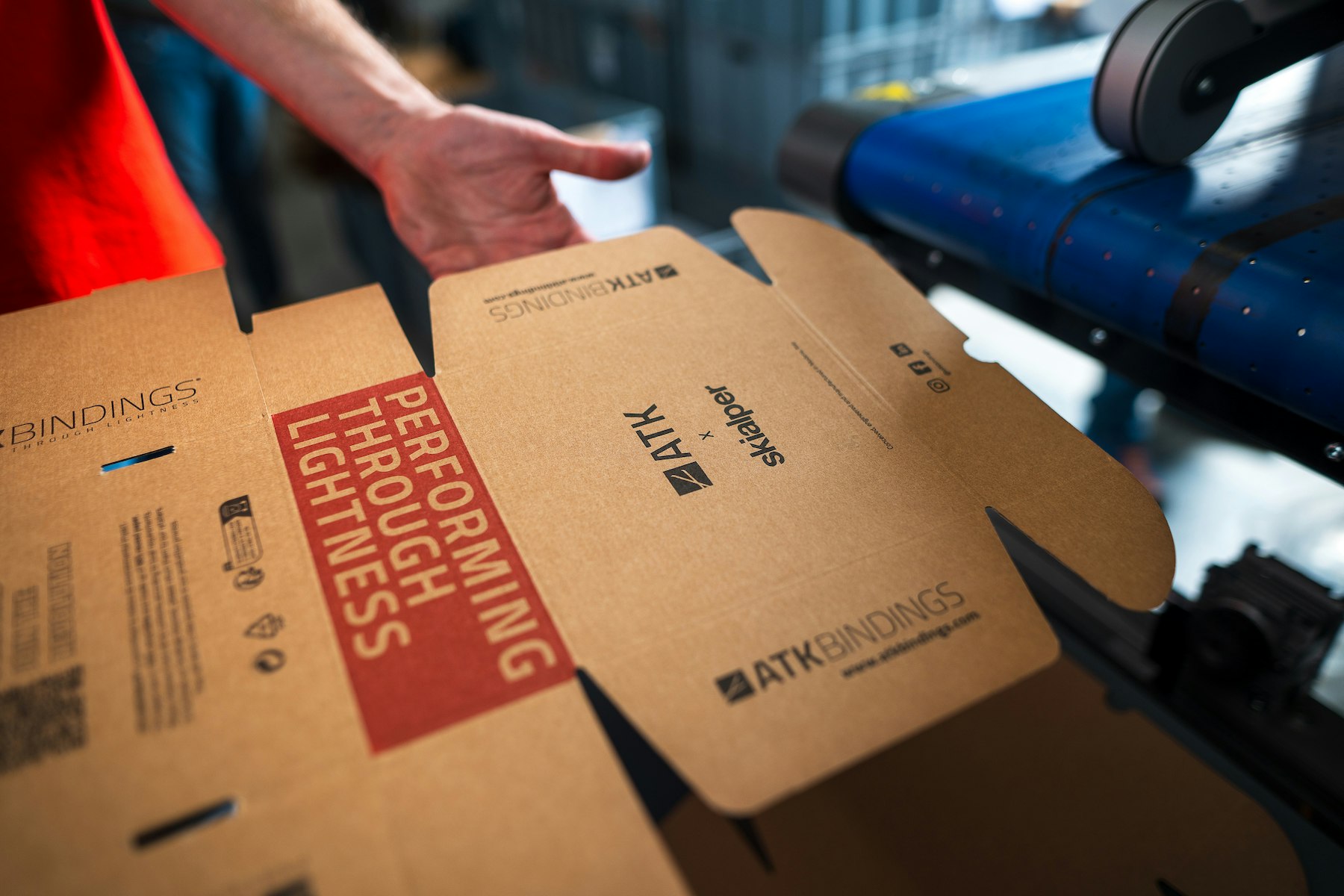
«È una domanda che ci facciamo da 15 anni, in realtà giorno dopo giorno ci rendiamo conto di quanto spazio ci sia davanti a noi, manca ancora tanta ricerca a livello di sicurezza tenendo gli stessi livelli di peso, oppure abbassando il peso e mantenendo il livello di sicurezza. Il nostro focus sugli attacchi full pin è mantenere la performance alzando il livello di sicurezza. Però ci rendiamo conto che il mercato dello scialpinismo è abbastanza limitato, siamo un’azienda leader e abbiamo l’intenzione di spendere il nostro know-how anche al di fuori, sempre rimanendo nel mondo della neve e della montagna, però pensiamo che sia egoista riservare questa capacità evolutiva limitatamente allo scialpinismo. Le linee di sviluppo saranno molto coerenti con la nostra missione e vicine alle caratteristiche del prodotto attuale: lascio a voi e alla vostra immaginazione…».
Davide Indulti
Condividi questo articolo