Attacchi amici dell'ambiente
Le nuove frontiere della sostenibilità e dell'economia circolare secondo ATK
- Fotografo: Giovanni Danieli
La sostenibilità secondo ATK
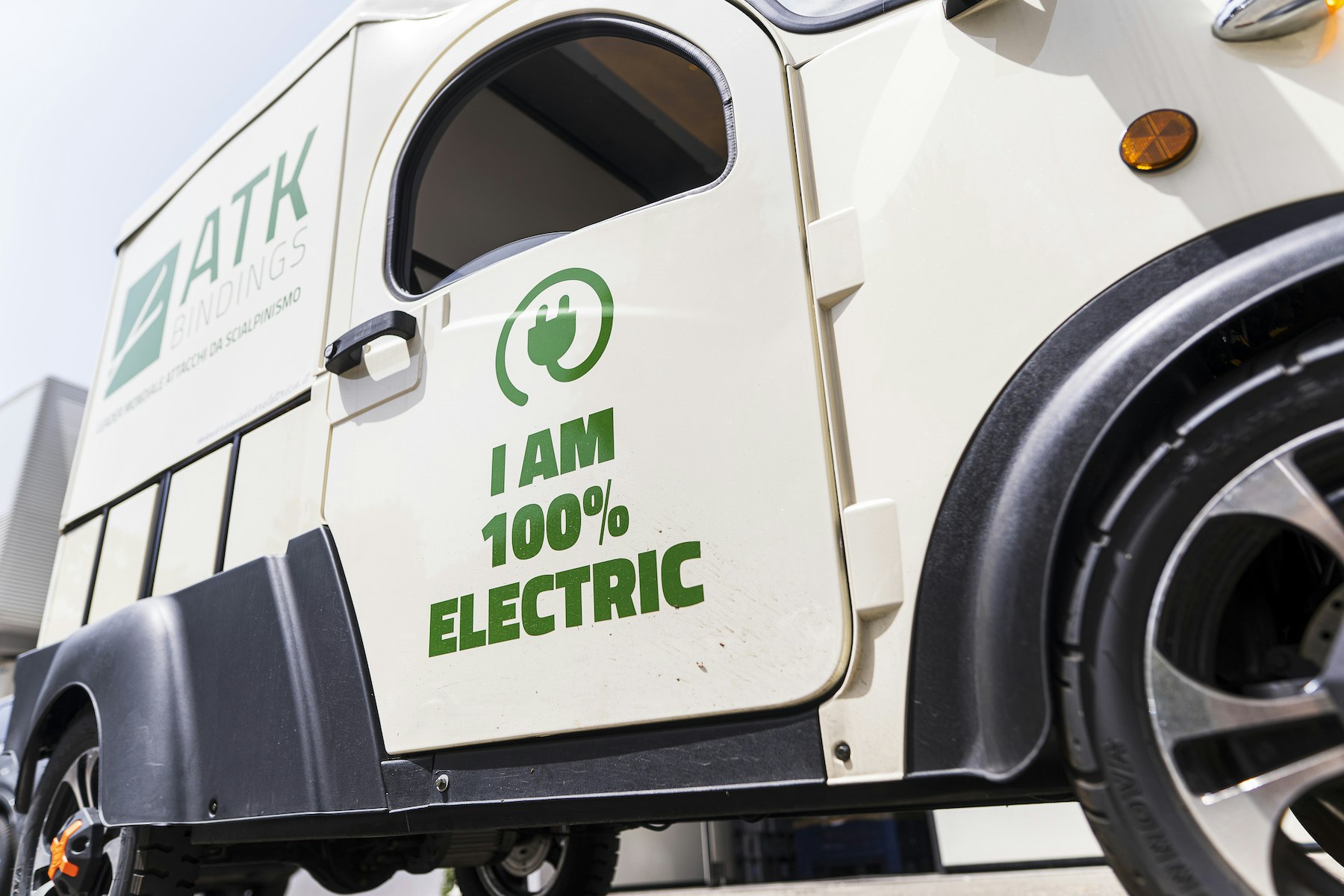
Quattro campi d'azione
I quattro pilastri dell'impatto ambientale causato dalla produzione degli attacchi di ATK Bindings sono la materia prima, la corrente elettrica, i liquidi lubrificanti/refrigeranti utilizzati per i macchinari a controllo numerico e l'acqua necessaria per il processo produttivo. Quattro problematiche che a Fiorano Modenese hanno iniziato ad affrontare già dalla nascita del marchio, partendo dalla considerazione che uno degli aspetti più importanti della sostenibilità e dell’economia circolare è il fine vita dei prodotti, che da sempre sono tutti completamente smontabili, un’operazione che ne agevola la riciclabilità.
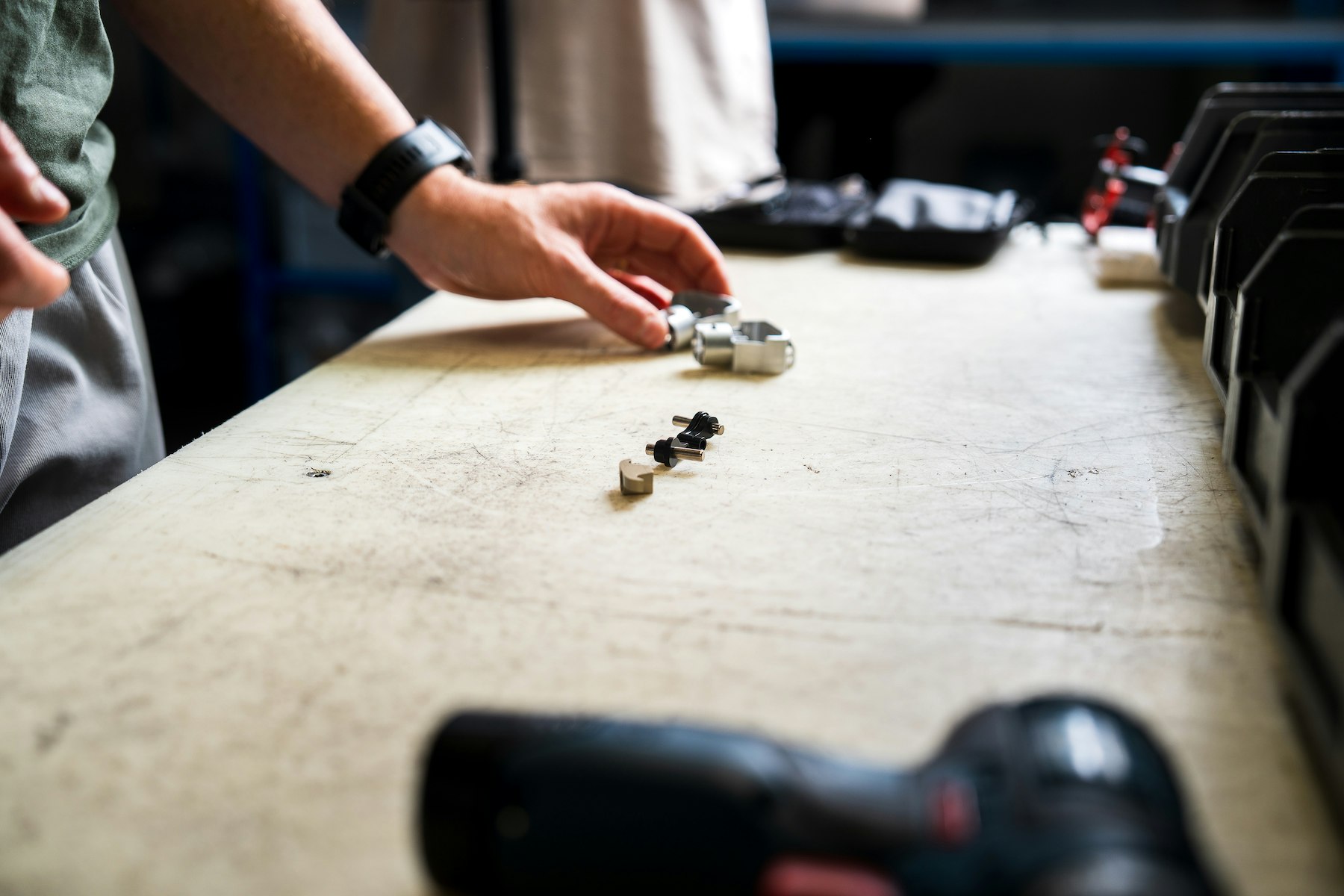
Davide Indulti
L’alluminio rappresenta circa il 90% della materia prima. In ATK riciclavano già gli scarti di produzione della lavorazione dal pieno che rappresentano circa il 90% della materia prima utilizzata nella produzione di un attacco. In pratica le migliaia di piccoli trucioli vengono pressate in cialde rotonde, che sono poi vendute ad aziende specializzate, ma da questo autunno si è entrati in una nuova fase che rende completamente circolare tutto il processo. «Il primo lotto di materia post consumo da riciclare partirà dalla nostra azienda nel mese di novembre verso uno dei più grossi produttori di alluminio europei che ci restituirà nuovo alluminio prodotto con il nostro materiale di scarto e con identiche caratteristiche meccaniche e livello qualitativo, il tutto certificato». La nuova tonnellata di alluminio prodotta permette di ridurre le emissioni di CO2 di circa sei volte. Un caso unico nel settore, nella direzione di quello che stanno cercando di fare i più grandi marchi dell’automotive. «Tutti i nostri competitor stanno andando nella direzione di impiegare materie plastiche per la produzione dei loro attacchi e questo chiaramente comporta cali di performance e caratteristiche in generale inferiori dal punto di vista della precisione, della qualità e della durevolezza nel tempo del prodotto, ma garantisce loro di poter certificare emissioni di CO2 molto inferiori rispetto all’alluminio o alle leghe metalliche, a maggior ragione accorciando la catena di produzione e riportando il processo produttivo più vicino a casa per minimizzare ancora le emissioni - dice Davide Indulti - Noi stiamo facendo l’opposto, vogliamo controllare completamente il nostro processo e non scendere a compromessi sulla precisione e la qualità, ma allo stesso tempo essere in grado di limitare l’impatto andando a creare un’economia circolare perché l'alluminio è uno dei pochi metalli che può essere riciclato all’infinito».
Davide Indulti
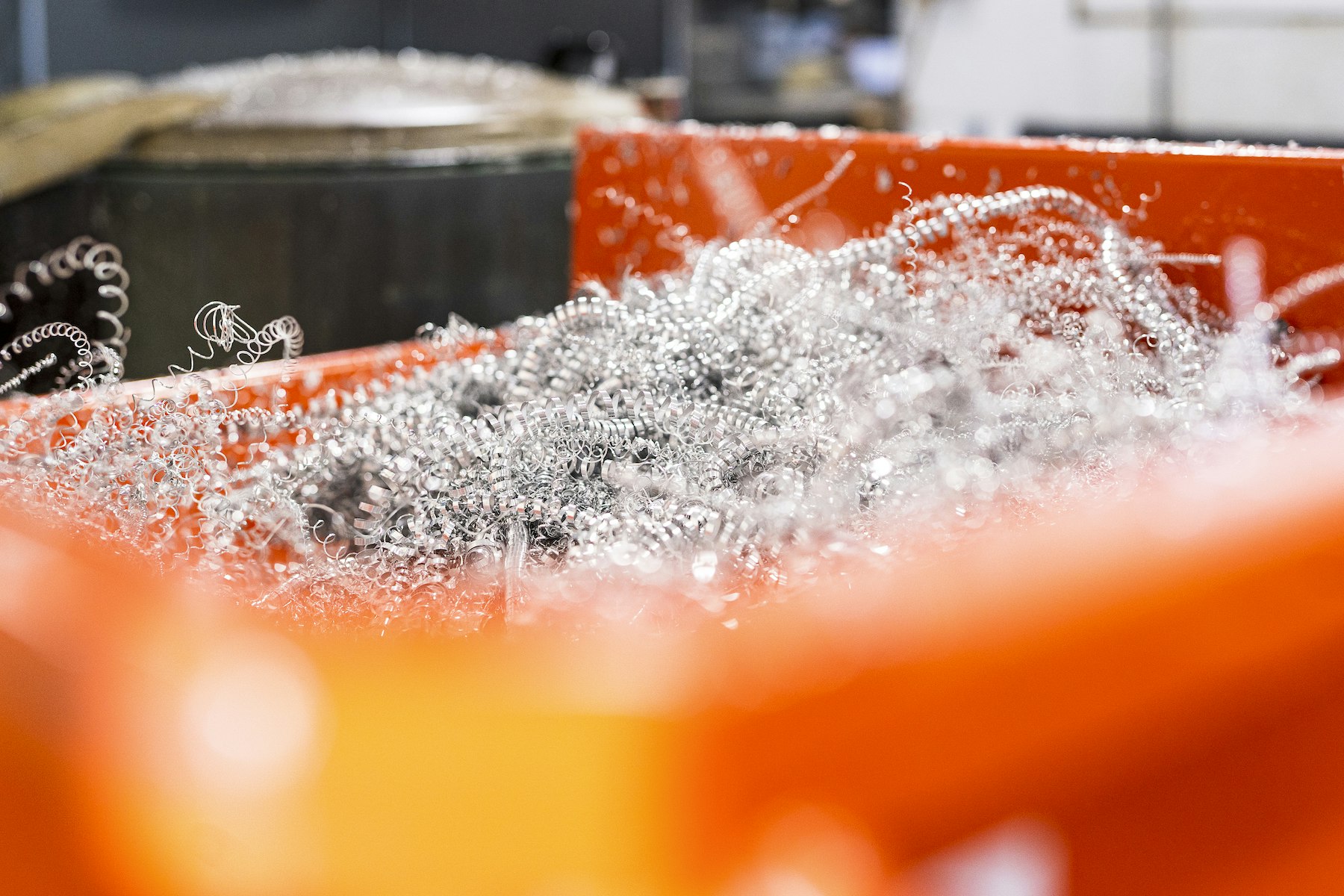
Davide Indulti
Per quanto riguarda l’energia elettrica utilizzata, già oggi sul tetto dello stabilimento c’è un impianto di pannelli fotovoltaici che fornisce circa il 15% della corrente utilizzata in un anno. «È un valore ancora basso, ci rendiamo conto che si può fare di meglio e nel nuovo stabilimento che stiamo progettando e realizzando a poco più di un chilometro da quello attuale avremo un impianto molto molto più grande, di circa un megawatt che renderà la nuova sede a energia negativa, vale a dire produrremo più energia di quanta ne sia necessaria per alimentare tutte i macchinari, l’illuminazione, gli uffici e le auto».
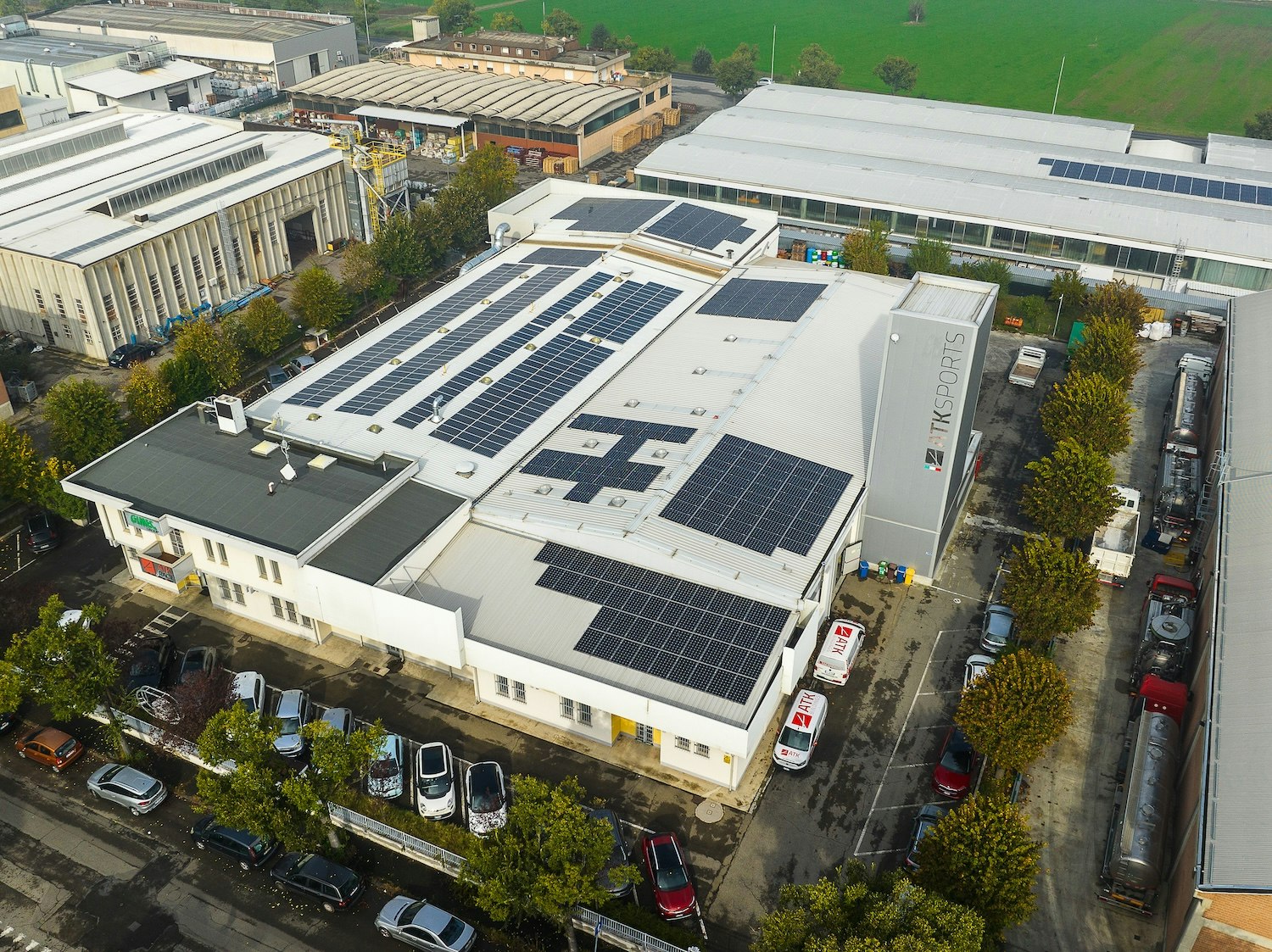
I lubrificanti impiegati nella lavorazione dal pieno sono prodotti chimici che servono per lubrificare i macchinari e garantire un buon funzionamento. Grazie a un particolare sistema di recupero, nei trucioli degli scarti di produzione ne rimane solo il 3% (percentuale che non richiede lavaggi chimici per la riciclabilità) e il resto viene nuovamente impiegato nella produzione, con benefici non solo per l’ambiente ma anche per i costi di produzione. Nel processo produttivo viene utilizzata anche acqua. «Siamo riusciti a rendere questo circuito completamente chiuso, non sprechiamo alcuna quantità di acqua, l’unica dispersione avviene per evaporazione» conclude Davide Indulti. Tutti questi accorgimenti, unitamente ai miglioramenti che saranno possibili dopo il trasferimento nel nuovo stabilimento, porteranno ATK a diventare la prima azienda produttrice di attrezzatura sportiva carbon neutral entro la fine del 2025.
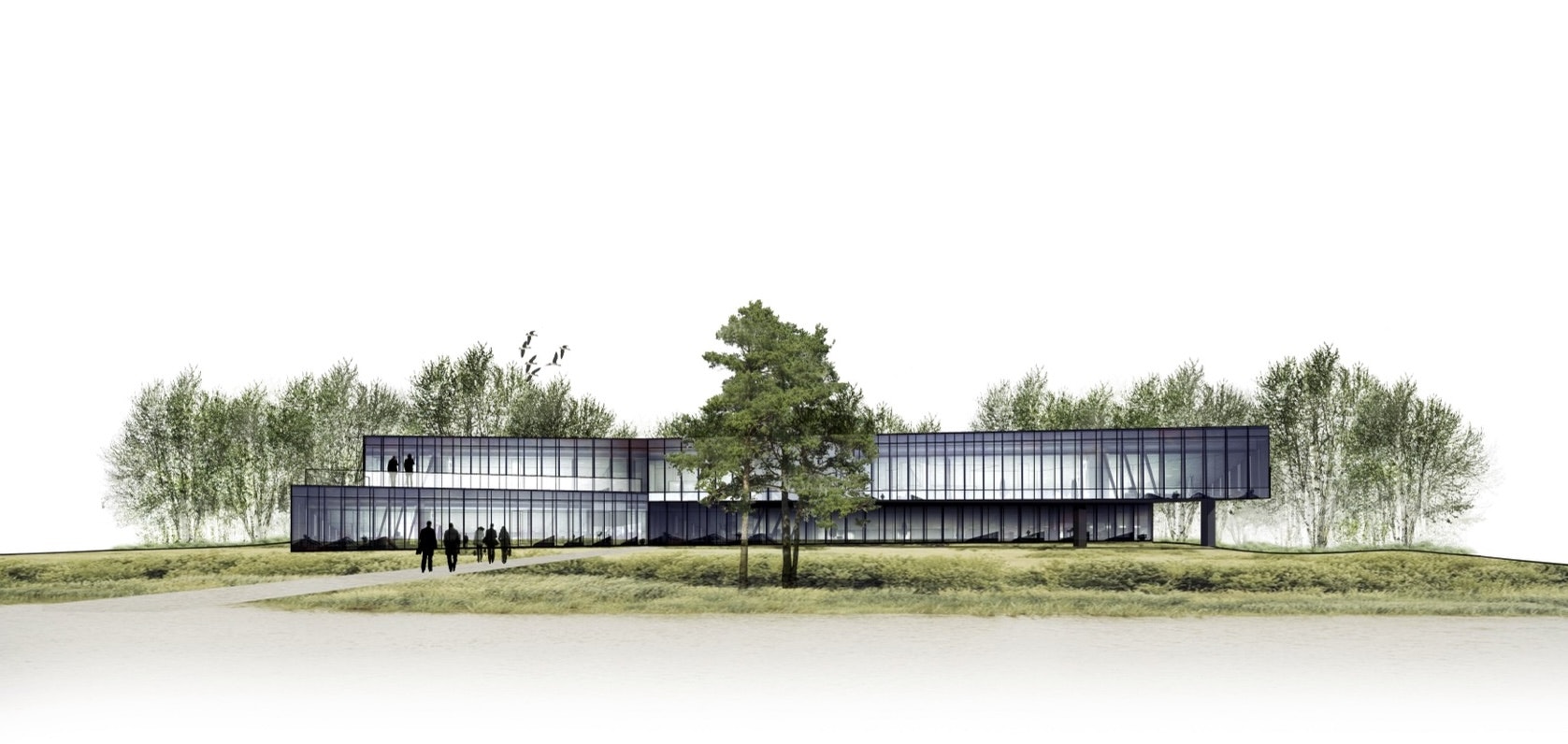
Condividi questo articolo