Hi-tech masterpieces
Performance through lightness
- Author: Claudio Primavesi
- Photographer: Giovanni Danieli
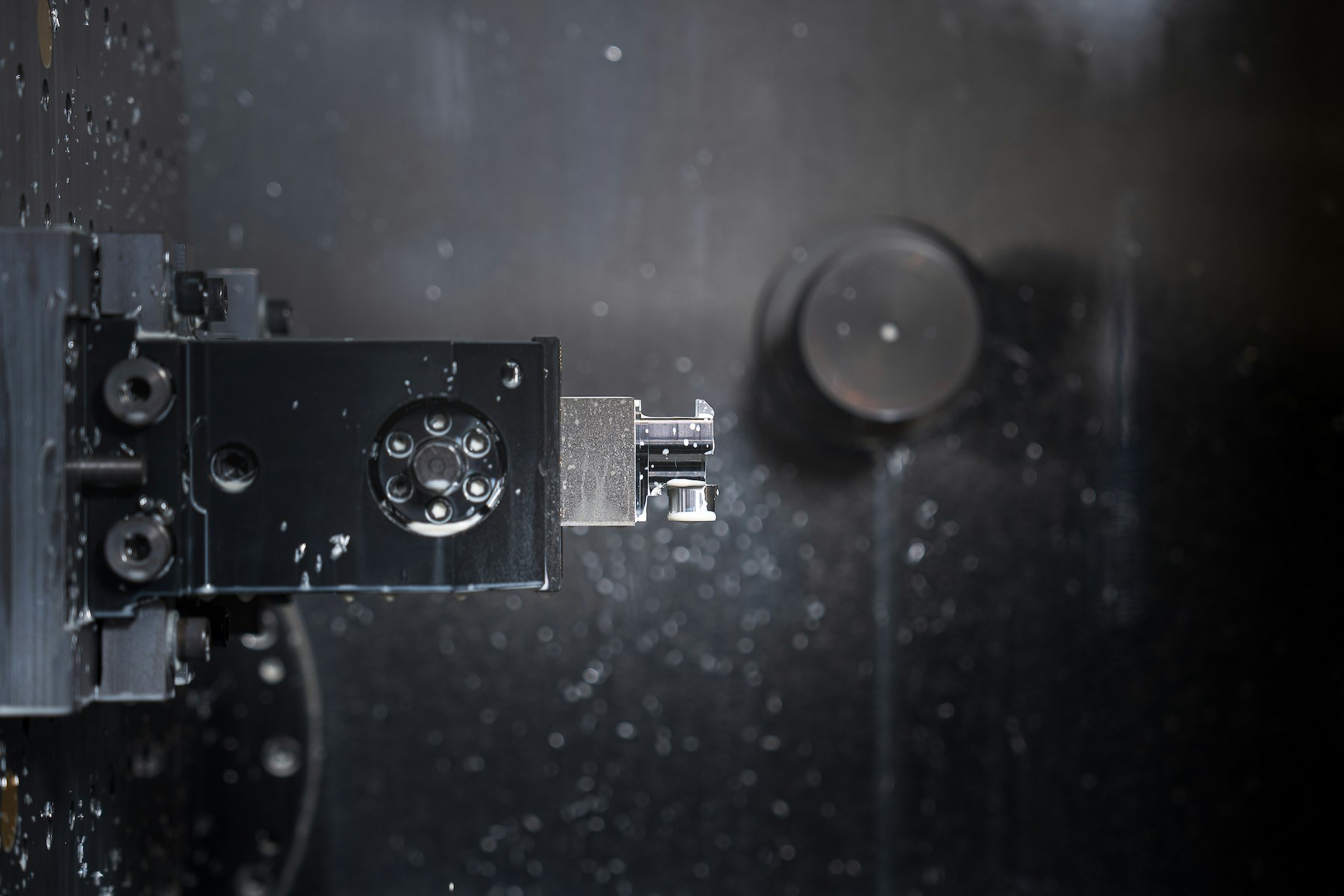
After witnessing the transformation of a block of aluminum into the heel piece of one of the signature models by the Modenese brand— based deep in the heart of Italy’s Motor Valley, the birthplace of Ferrari—you realize that the message in ATKs ad campaign is true. A binding milled from one piece really is like a sculpture. The difference being that instead of a hand wielding a chisel, there’s a high-tech five-axis machine doing the carving. Nevertheless the two processes have much in common. As the machine carries out what the operator, the artist in this case, has painstakingly programmed it to do. The realization dawns on us when the Skialper logo begins to take shape in front of our incredulous eyes. Somebody had to dream up the idea, sketch it on paper and then design it on a computer.
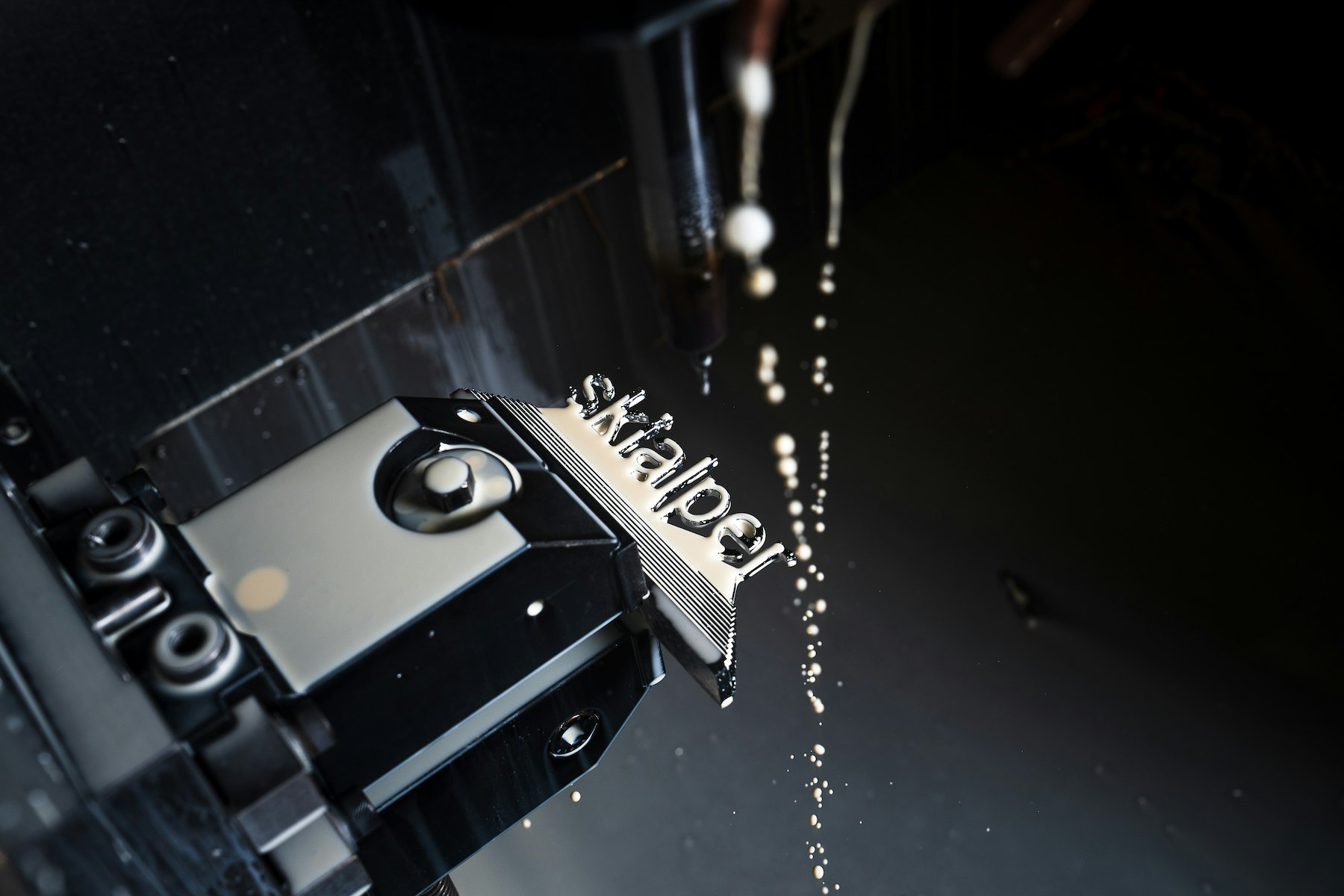
Ultimately, the secret to this miracle of Italian entrepreneurship lies here: introducing skills and technology from aerospace and automotive engineering into the world of ski touring and freeride. David Indulti, CEO of ATK bindings, gets straight to the point: “At the heart of the ATK mission is the search for lightweight, extreme precision that only a CNC machine can produce.” A process that manufactures high-quality items at an affordable cost thanks to the optimization of the manufacturing process and reuse of scrap and other necessary materials like lubricant. An advantage that, in the vision of the future that the brand has had since the production of their very first binding, could paradoxically reveal itself to be a problem. As Davide Indulti explains, the ghost of a smile on his lips: «The dream is to get to the point where we recycle the aluminum from old bindings to make new ones. But we also realize that the value of our bindings stems from the fact that, when maintained correctly, they work for a long time, which creates an obstacle».
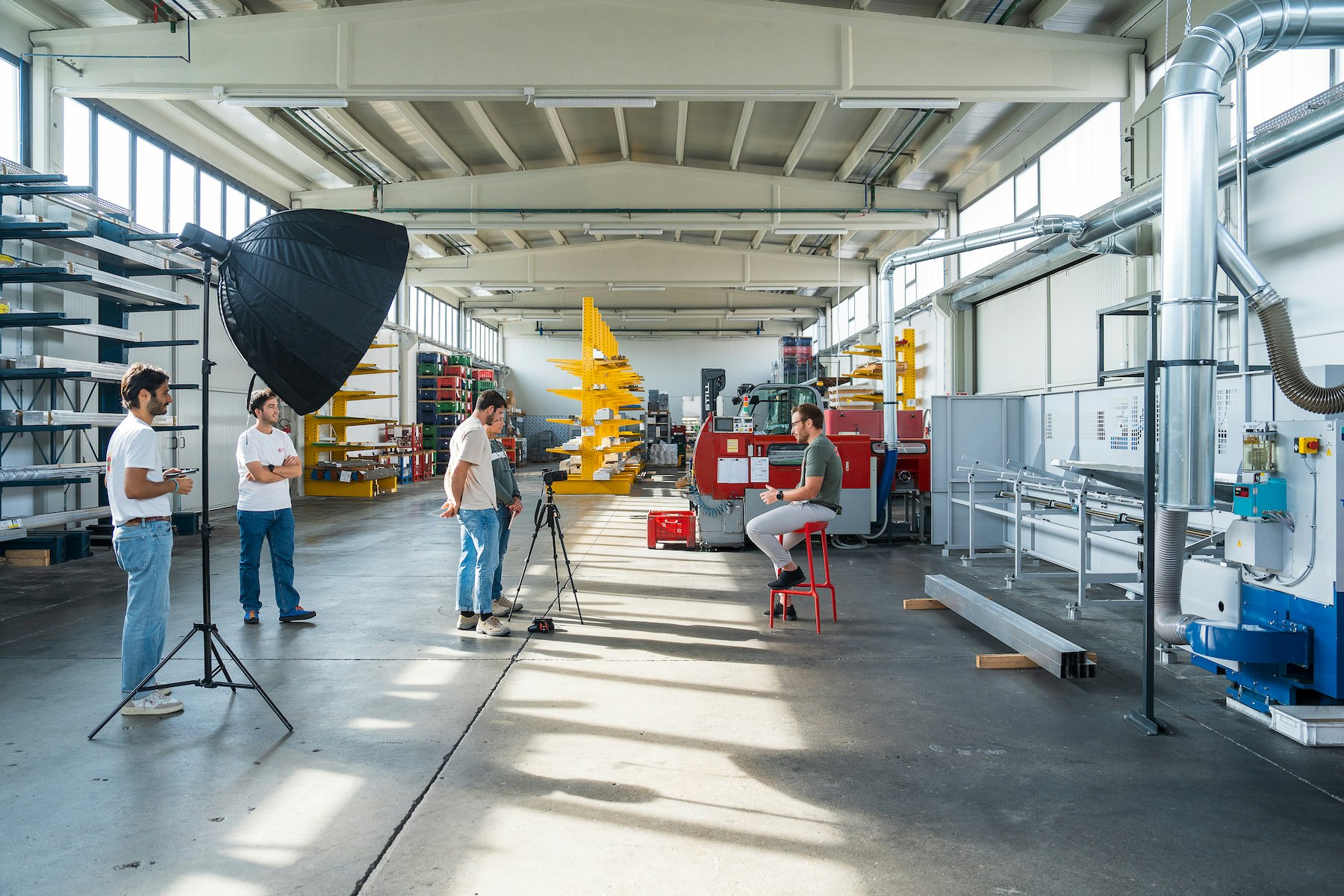
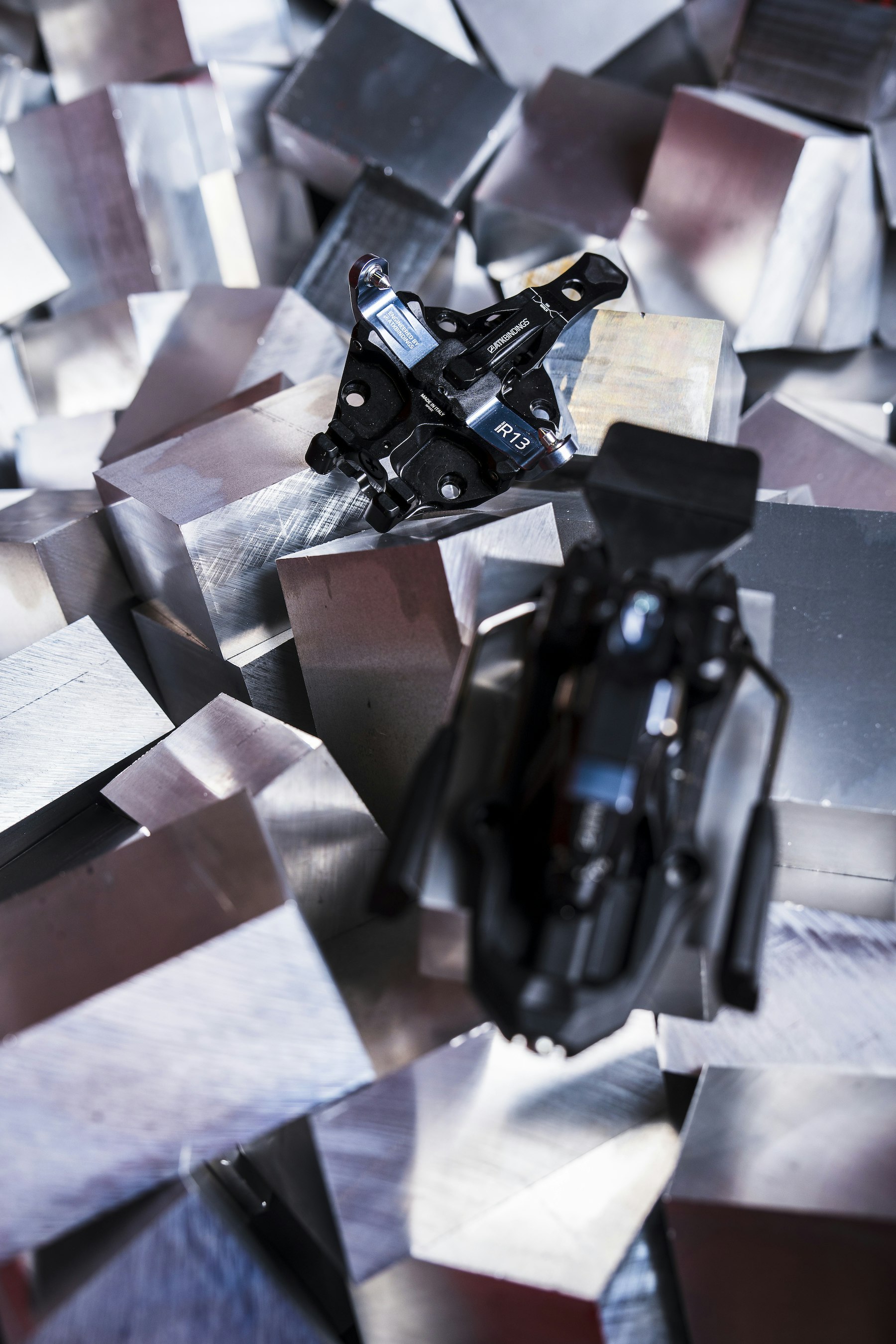
Though it’s not such a big obstacle when you think that the basic rule of sustainability is that the product with the least impact is the one that lasts longest. It’s the paradox of a groundbreaking modern vision, which has led this brand from Italy’s tech hub, a stone’s throw from its agricultural heartland, to become a global leader in pin bindings; fusing the spirit of the mountains with that of one of the most important industrial areas in the world.
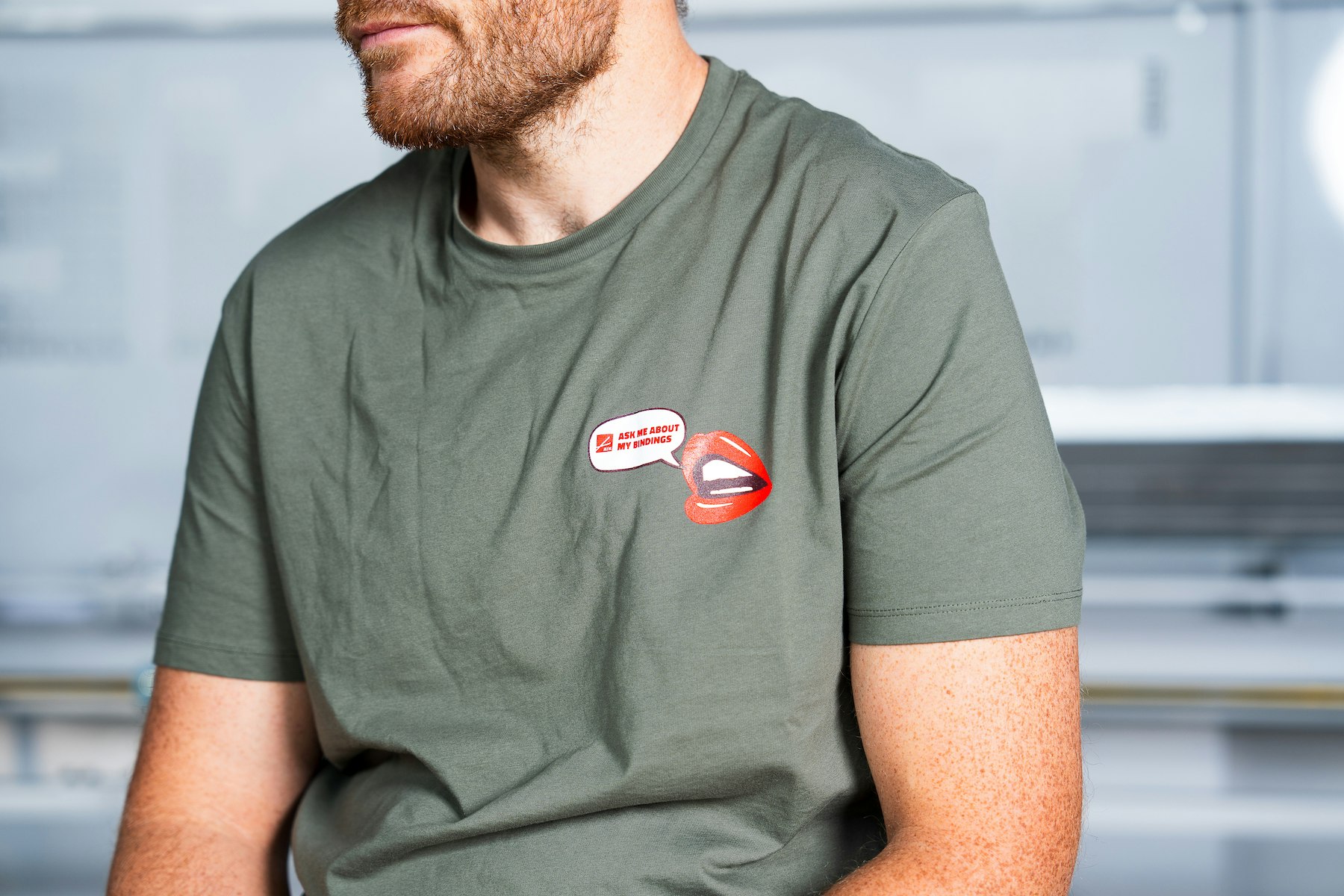
ATK’s slogan says a lot about their philosophy: Performing through lightness. From the early days of ATK—when reducing the weight of a race model by 10 grams using a technology hitherto unused in the sector was nothing short of revolutionary—‘lightness’ has remained inextricably linked with the brand’s mission, even now when it is no longer an end in itself, but where it contributes to the overall skiability of the product. Performance through lightness.
Davide Indulti
A concept that is easy to express, but difficult to realize. As it’s taken 15 years of continuous development while remaining true to the original idea: the pin binding. There are patents like the CAM Release System that makes a heel piece almost as stable as a step-in binding. There are warehouses full of aluminum blocks from the best suppliers that are broken down into 20–45 pieces used to make bindings. There are tens of millions of euros invested each year in new equipment, with 15 mills for one-piece machining. But there is also a huge amount of professionalism and an average age of 30. The necessary know-how to manage the whole process start to finish. And eyes fixed firmly on the future.
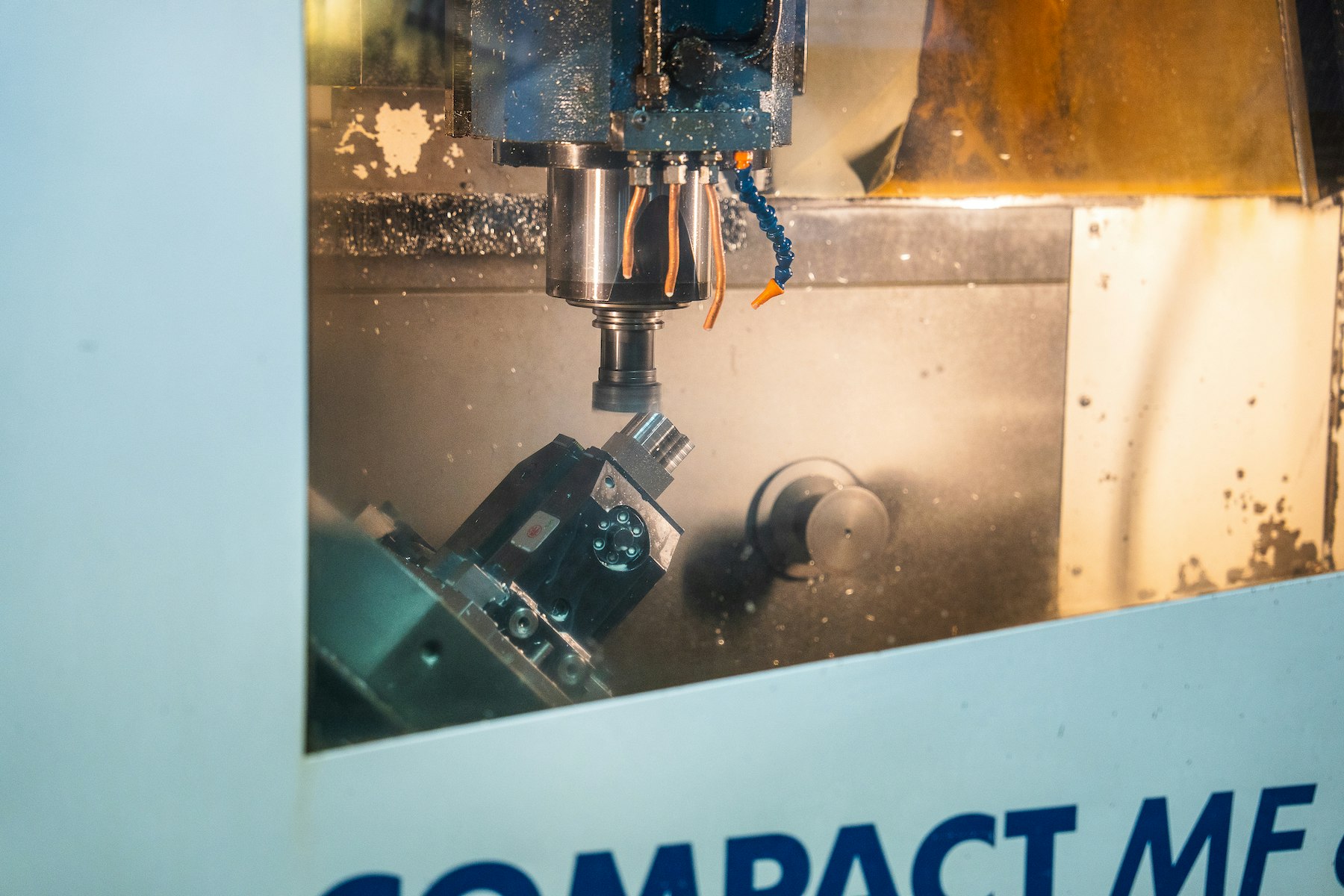
We had already been to the ATK factory a year ago. Twelve months later we saw two new 3D printers able to produce the prototype of a binding in aluminum and stainless steel overnight. A binding ready to hit the snow, weight difference aside. And a machine that produces the exact number of boxes necessary for the production lot of a specific binding model, avoiding waste and errors. A reduction in waste also guaranteed by using 86% recycled carboard that is 100% recyclable, and labels only when strictly necessary. Even the mounting instructions are printed on the box. It looks like there is nothing more left to do. Or at least it looks that way...as Davide Indulti confirms when seeing us off from the doorway of the assembly line.
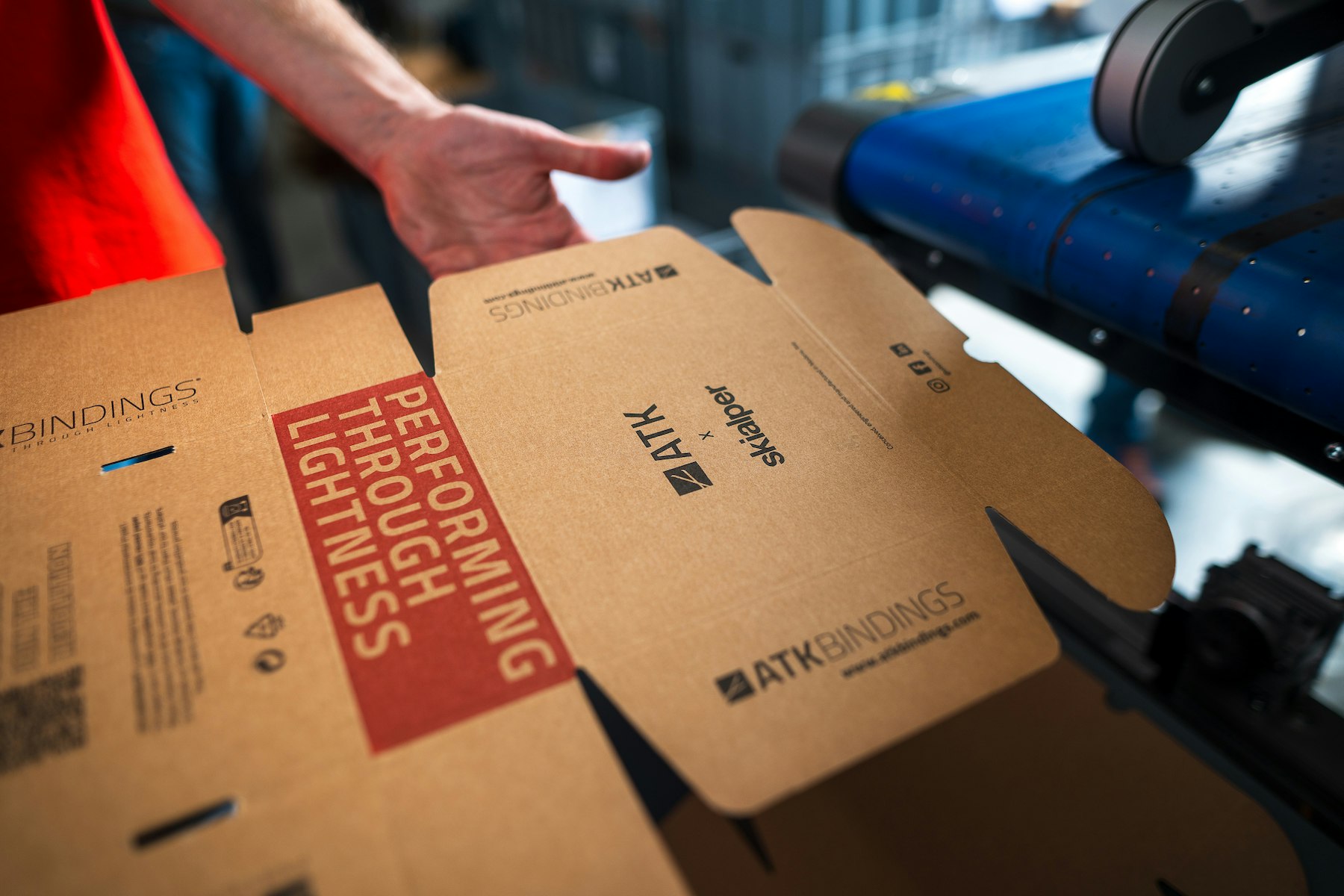
«It’s a question we’ve been asking ourselves for 15 years; in reality, day after day we realize how much road we still have to travel. There’s a big gap in research into safety when maintaining the same levels of weight, or lowering the weight and maintaining the same levels of safety. Our focus where full pin bindings are concerned is to maintain the same levels of performance while increasing safety. That said, we realize that the ski touring market is fairly limited, we’re a leading company in the industry and we intend to also use our know-how outside it, while remaining in the mountain sports sector. We think it would be wrong to limit this development potential to ski touring alone. The direction we take will be fully in line with our mission and current project: I’ll leave the rest to your imagination...».
Davide Indulti
Share this article