Machining from one piece
Accuracy first
- Author: Claudio Primavesi
- Photographer: Giovanni Danieli
The production process that changed the AT bindings world
Machining from one piece is usually linked to the aerospace or motorsports industries as the costs are much higher than other manufacturing processes like stamping, plastic injection molding or forging, which are used by other binding manufacturers. The CNC machines used by ATK at their state-of-the-art factory—one of the most advanced in Italy’s Motor Valley, which in turn is on the cutting edge of this technology—guarantee absolute precision in the manufacturing of components. Stamping, injection molding and forging just don’t deliver the same quality in terms of (low) weight and aesthetics.
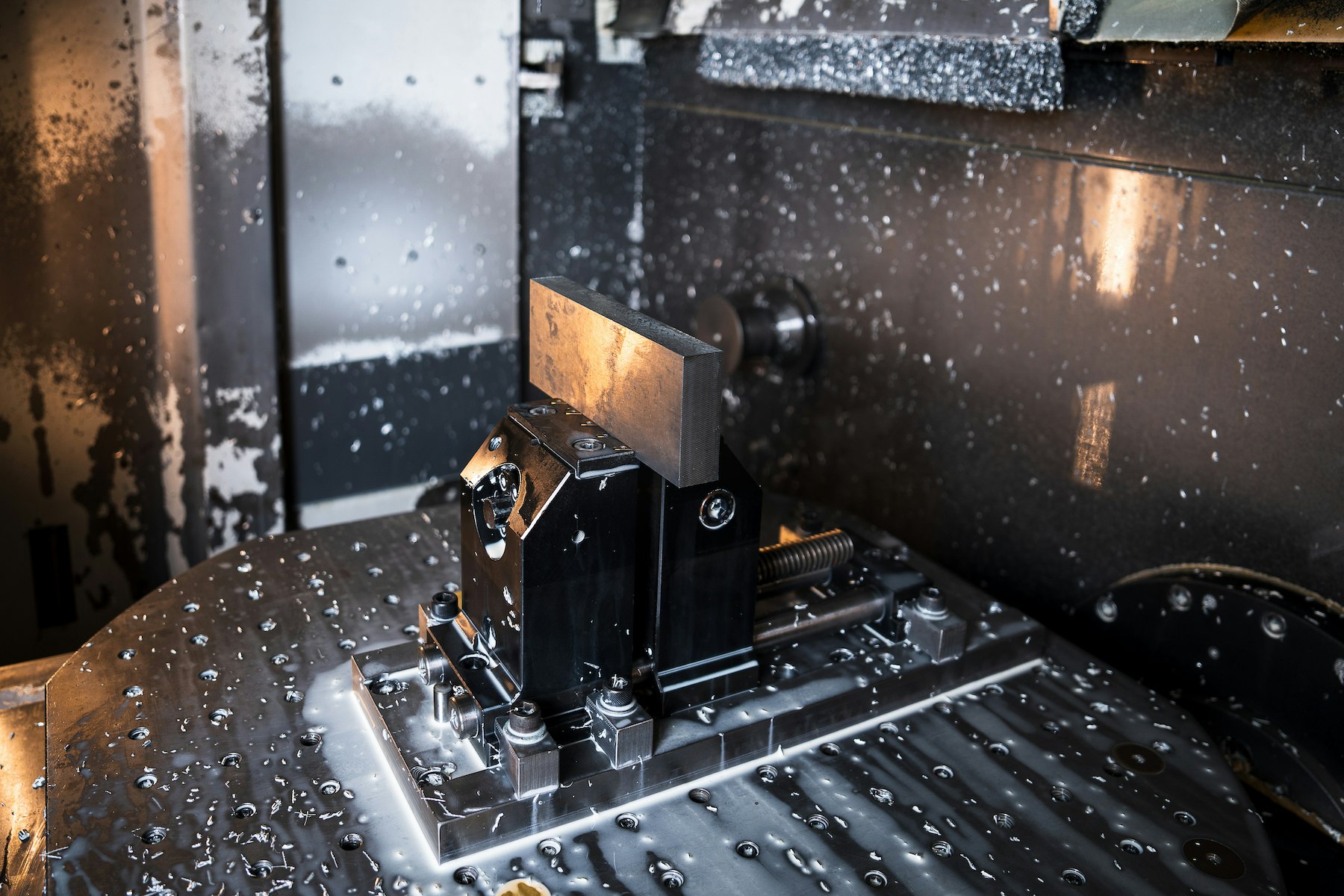
The end result is a seamless connection between the skier, their boot and the snow. The closer you get to the top end of the performance scale, like racing, the more extreme the results: the heel piece of the Revolution World Cup weighs 14 g (0.5 oz), just 6% of the original block of aluminum 7075 (Ergal). The procedure is incredibly quick, just program the project into the terminal and the machine will carry it out to the letter. We watched in awe as we saw the Skialper logo take shape in front of our very own eyes. Between the initial project and the final result, rigorous quality control measures are implemented using lasers to measure the finished components. The process is carried out on the first and last items, as well as randomly throughout; in this way it’s possible to trace back to any eventual problems.
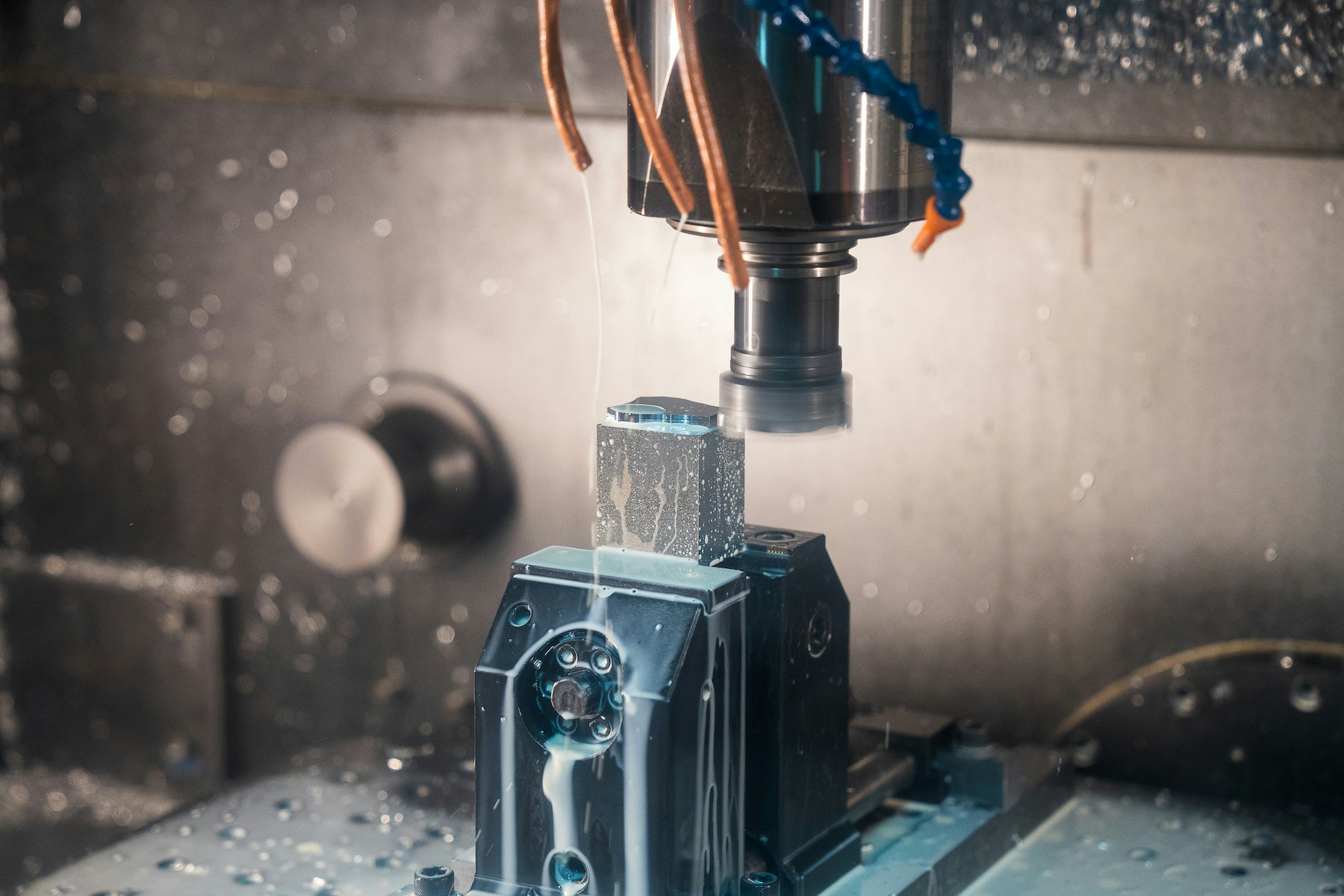
Share this article