Eco-friendly bindings
The new frontiers of sustainability and circular economy according to ATK
- Photographer: Giovanni Danieli
ATK's way to sustainability
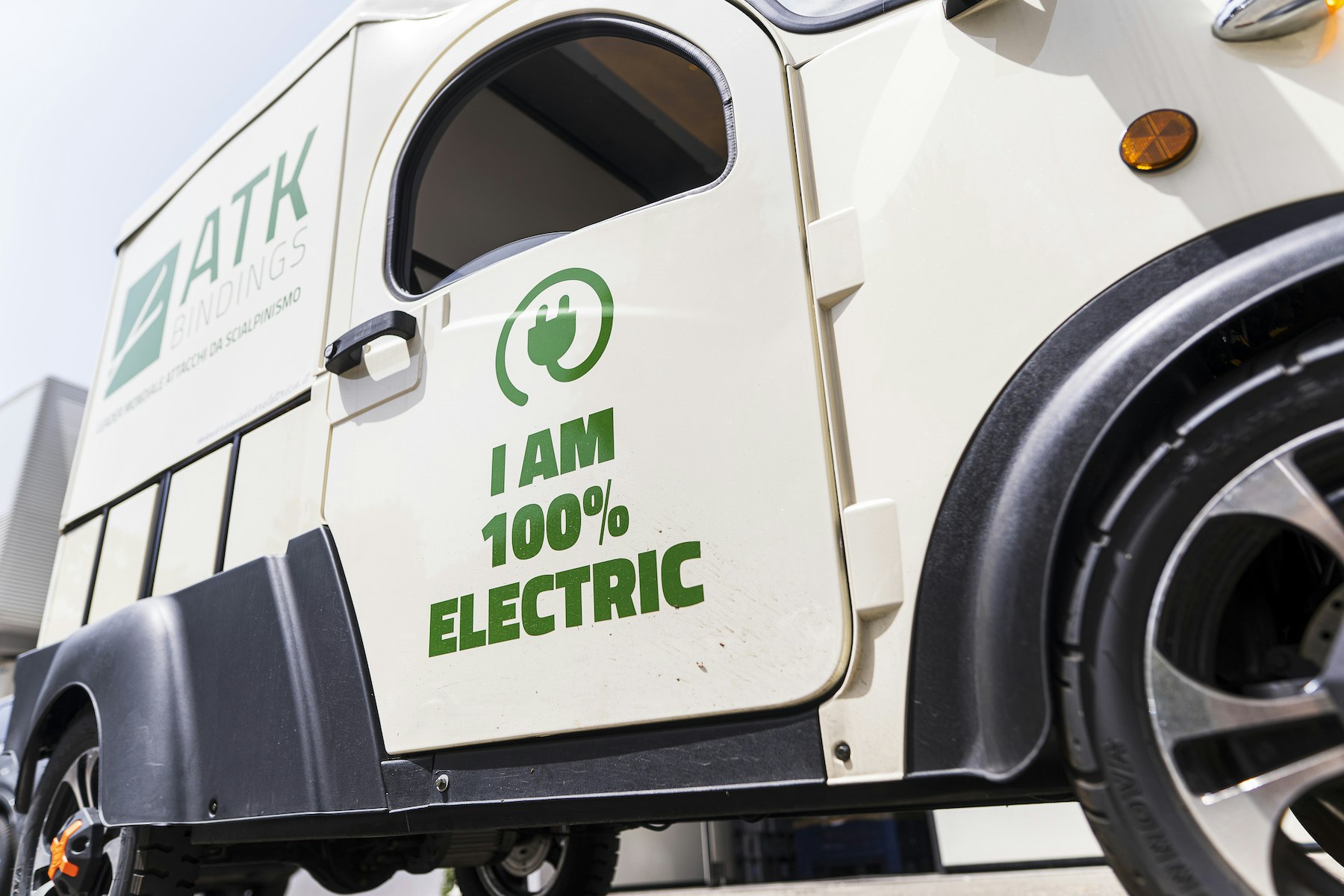
Four areas of action
Raw materials, energy usage, CNC machine lubricants and refrigerants, and water used in the production process are the four main contributors to the environmental impact of ATK bindings. Four problem areas that, at the brand’s HQ near Modena, they have been trying to tackle since the company was founded. One of the most important aspects of sustainability and the circular economy is the end of a product’s life cycle, so ATK bindings have always been easy to dismantle, and therefore recycle.
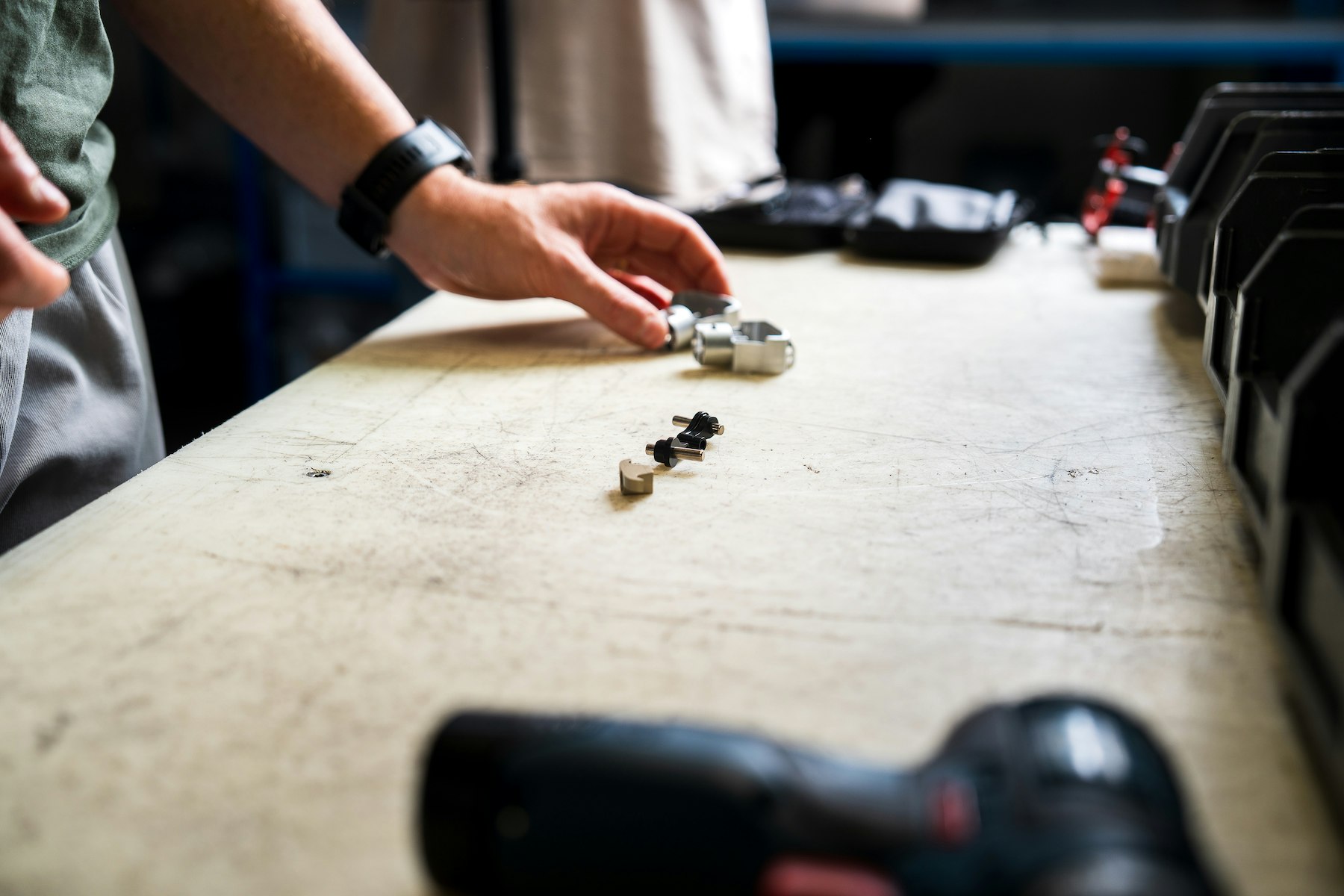
Davide Indulti
Aluminum accounts for around 90% of the total raw materials used. At ATK they were already recycling the scrap from the milling process, the shavings pressed into round briquettes then sold to specialist companies. However, as of this autumn, the brand has made the process entirely circular. “The first batch of post-consumer material to be recycled will leave our factory in November, destined for one of the biggest aluminum manufacturers in Europe, who will send us back new aluminum made from our own waste material, of the same quality with identical mechanical properties, and fully certified.” This newly recycled ton of aluminum will lower CO2 emissions sixfold. They are the only binding manufacturer to take this step, moving in the same direction as the biggest car manufacturers. “All our competitors are using more plastic in their binding production to the detriment of performance and causing a general drop in precision, quality and durability, but it means they can record much lower CO2 emissions compared to aluminum and metal alloys, as well as shorten their supply chain and bring their production process closer to home to further reduce emissions,” says Davide Indulti. “We are doing the opposite, we want to have complete control over our processes and not compromise on precision and quality, while at the same time being able to limit our environmental impact by creating a circular economy, as aluminum is one of the few metals that can be infinitely recycled.
Davide Indulti
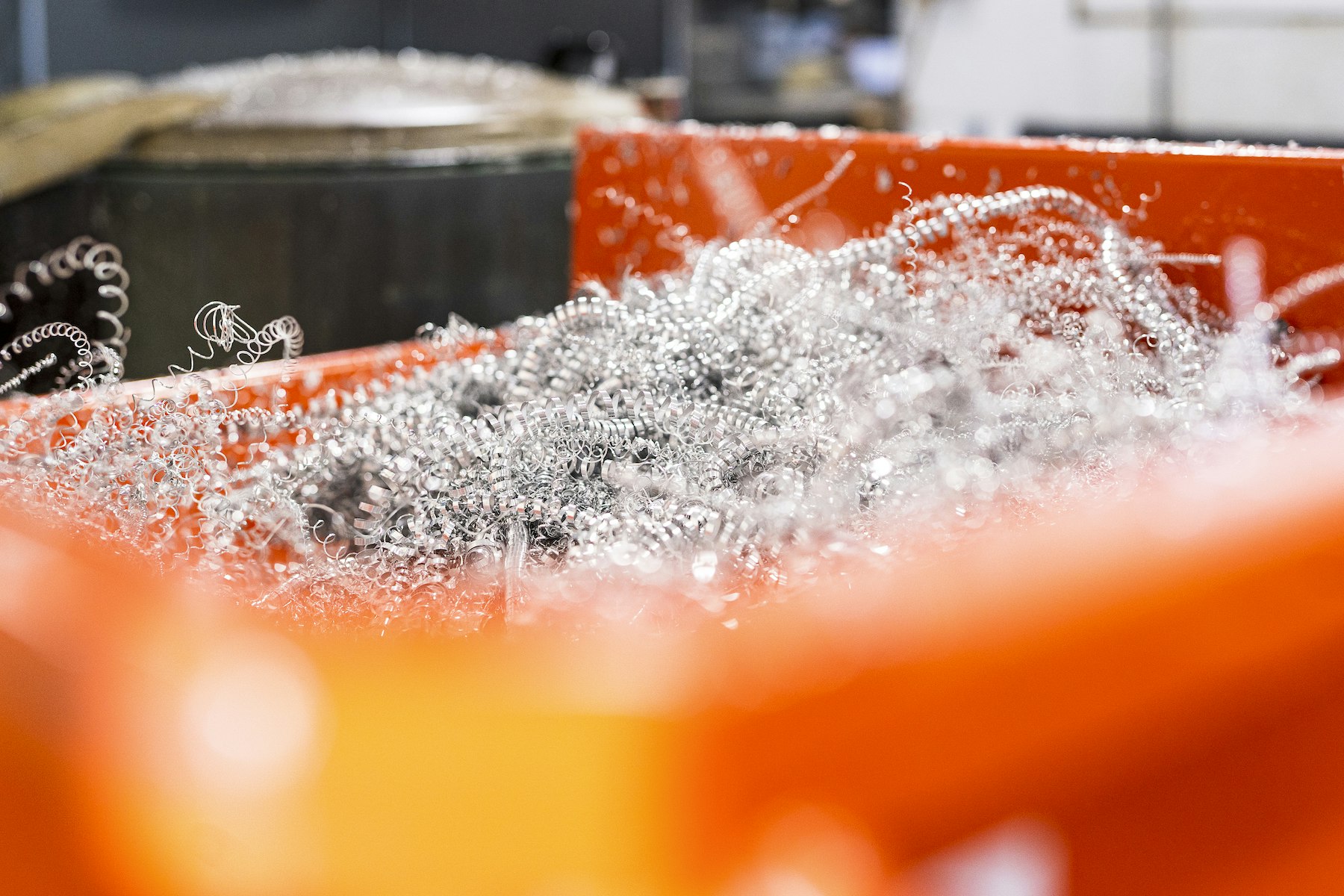
Davide Indulti
As for energy usage, we already have solar panels on the roof of our factory that supply around 15% of our yearly energy needs. “We realize that this is a small amount and we need to do better. At our new factory, which is being built just under a mile from the current one, we will have a much bigger one megawatt solar power plant, which will make the new building climate neutral. In other words, we will produce more energy than we need to run our machines, lighting, offices and cars.
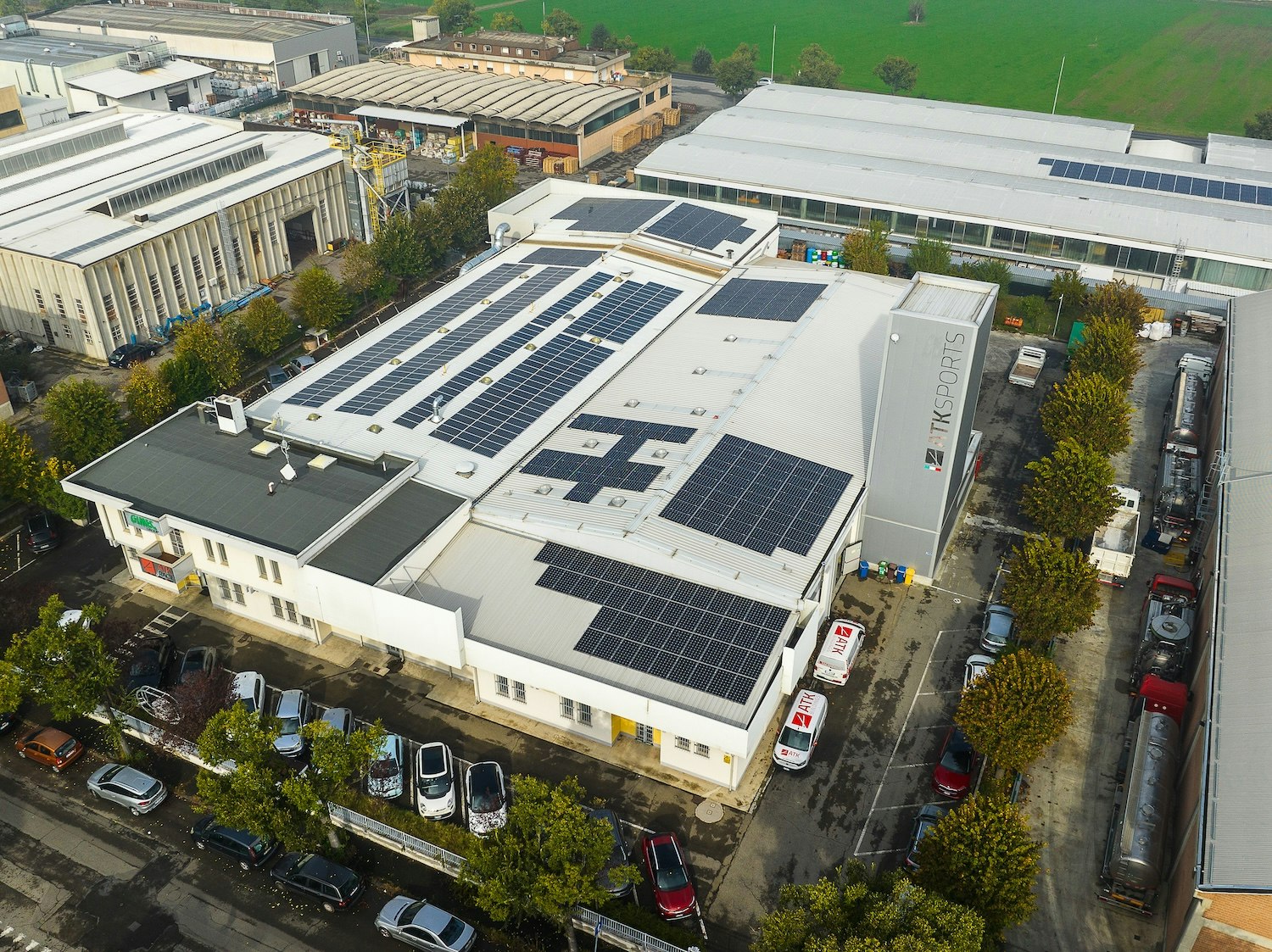
The lubricants used for milling are chemical products required to lubricate the machines so they run smoothly. Thanks to a special kind of recovery system, only 3% remains in the milling waste (a percentage that doesn’t require chemical washing before recycling), and the rest can be used again in production, with advantages not just in environmental terms, but also for production costs. The production process also uses water. «We have been able to completely close this loop so we don’t waste a single drop, the only water that we release into circulation is that which evaporates» says Indulti. All these measures, together with the improvements that will come with the move to the new factory, will lead ATK to become carbon neutral by the end of 2025.
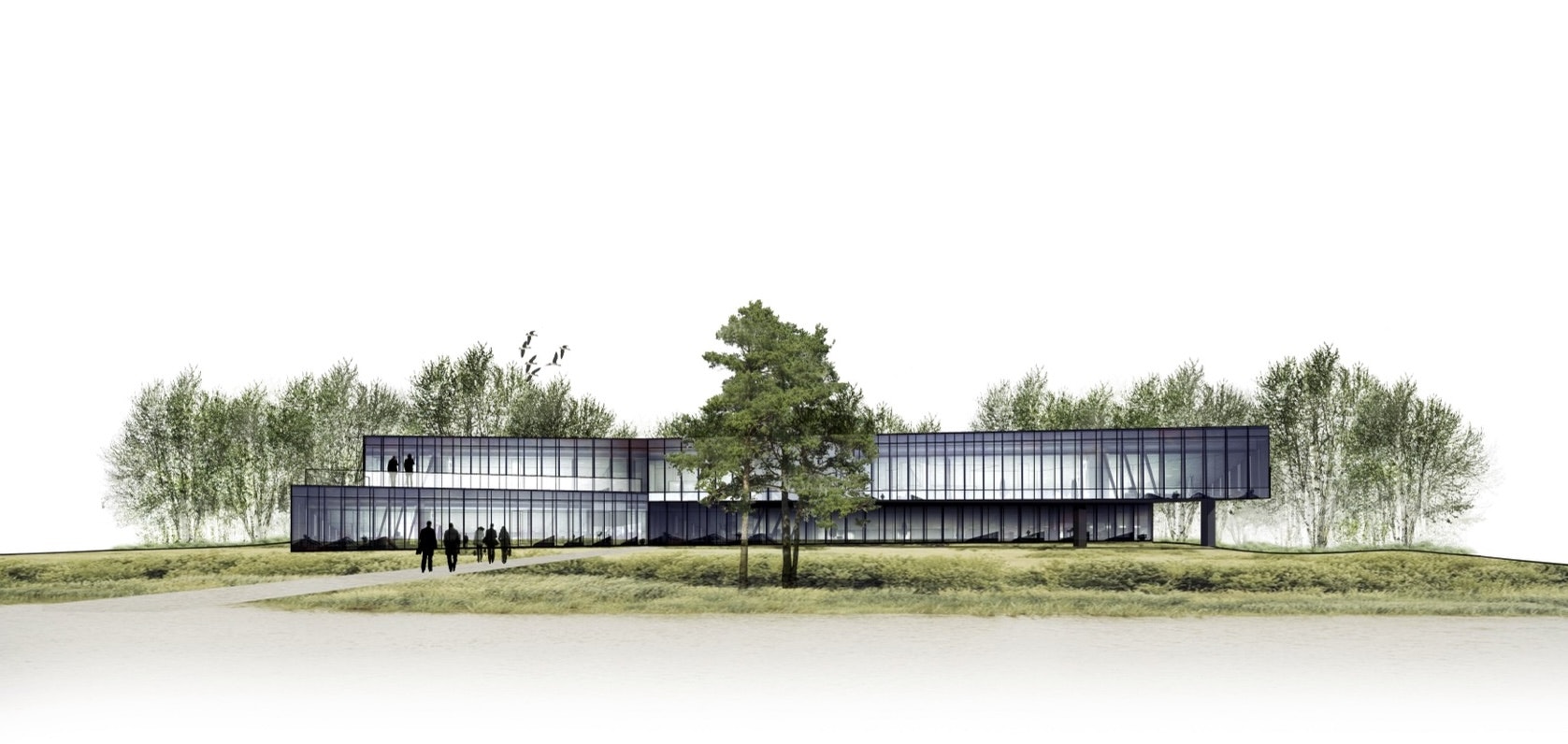
Share this article